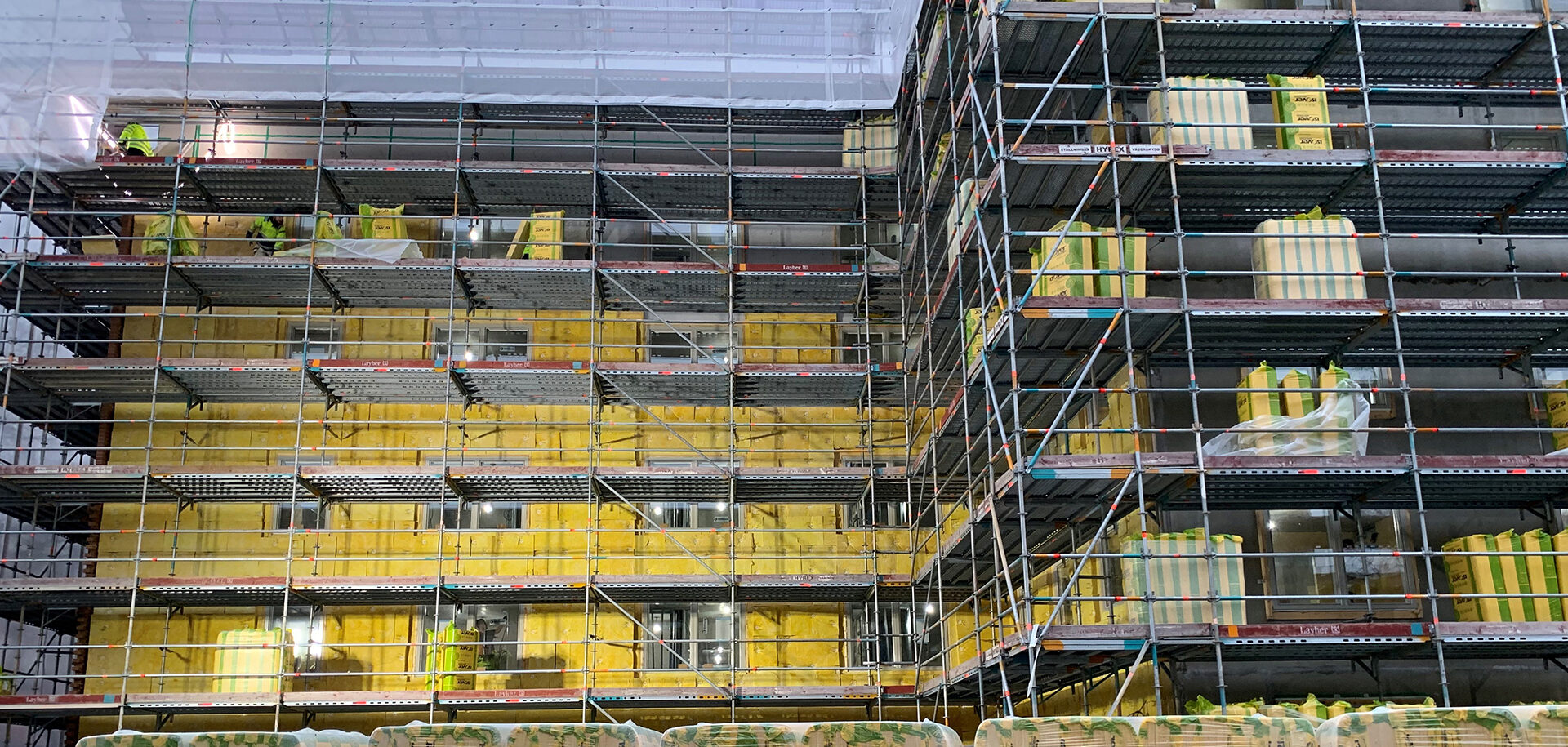
La protection des machines contre les défaillances à la clé d’un isolant performant
Les équipes de maintenance de Saint-Gobain Isover exploitent le potentiel du digital pour fiabiliser la production d’un produit concourant aux économies d’énergie.
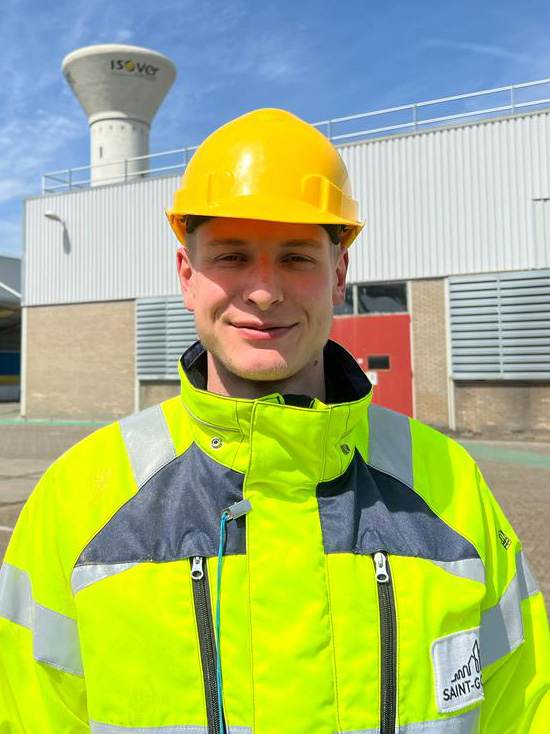
Comment vivre et travailler dans le confort sans réchauffer l’atmosphère ? Les bâtiments sont responsables de près de 40 % des émissions mondiales de CO2 associées à l’énergie. Les deux tiers sont émis par l’énergie consommée pour chauffer ces constructions l’hiver et les rafraîchir l’été.
Si la planète veut atteindre ses objectifs de réduction des gaz à effet de serre, elle doit accélérer la transition vers des bâtiments plus écologiques et plus efficaces sur le plan énergétique. Cette démarche nécessitera des investissements dans de nouvelles technologies, telles que les panneaux voltaïques aménagés sur les toits et les pompes à chaleur alimentées par de l’électricité renouvelable. Mais l’un des moyens les plus efficaces de réduire l’empreinte carbone d’une construction est l’isolation thermique, et c’est aussi l’un des plus simples.
Une bonne isolation thermique empêche les déperditions de chaleur à travers les murs et les toits. C’est une méthode simple, éprouvée et d’un bon rapport coût-efficacité. Dans la plupart des bâtiments, les propriétaires amortissent le coût des travaux d’isolation en quelques années seulement grâce aux économies réalisées sur leurs factures d’énergie.
Située à Etten-Leur, aux Pays-Bas, l’usine Isover de Saint-Gobain est une spécialiste de l’efficacité énergétique depuis 1962. Elle fabrique environ 45 000 tonnes de laine de verre par an sous forme de panneaux et rouleaux pour l’isolation des toitures et un produit à base de fibres qui peut être injecté dans les murs creux ou soufflé dans les combles.
Elle abrite trois lignes de production de laine de verre, ainsi qu’une quatrième qui fabrique le matériau en fibre de verre servant de revêtement à certains de ses produits. Bas Beishuizen est ingénieur de la maintenance sur le site. Sa mission est de veiller à ce que les équipements de ces lignes fonctionnent en toute fiabilité et efficacité.
La production de laine de verre étant une activité à grande vitesse, à grands volumes et très énergivore, l’équipe de maintenance doit veiller sur de nombreuses machines. « L’ensemble du site compte 57 équipements stratégiques. Ce sont principalement des pompes et des ventilateurs, assez volumineux dans certains cas. Nos plus gros ventilateurs sont alimentés par des moteurs de 500 kilowatts, par exemple. »
Comment vivre et travailler dans le confort sans réchauffer l’atmosphère ? Les bâtiments sont responsables de près de 40 % des émissions mondiales de CO2 associées à l’énergie. Les deux tiers sont émis par l’énergie consommée pour chauffer ces constructions l’hiver et les rafraîchir l’été.
Si la planète veut atteindre ses objectifs de réduction des gaz à effet de serre, elle doit accélérer la transition vers des bâtiments plus écologiques et plus efficaces sur le plan énergétique. Cette démarche nécessitera des investissements dans de nouvelles technologies, telles que les panneaux voltaïques aménagés sur les toits et les pompes à chaleur alimentées par de l’électricité renouvelable. Mais l’un des moyens les plus efficaces de réduire l’empreinte carbone d’une construction est l’isolation thermique, et c’est aussi l’un des plus simples.
Une bonne isolation thermique empêche les déperditions de chaleur à travers les murs et les toits. C’est une méthode simple, éprouvée et d’un bon rapport coût-efficacité. Dans la plupart des bâtiments, les propriétaires amortissent le coût des travaux d’isolation en quelques années seulement grâce aux économies réalisées sur leurs factures d’énergie.
Située à Etten-Leur, aux Pays-Bas, l’usine Isover de Saint-Gobain est une spécialiste de l’efficacité énergétique depuis 1962. Elle fabrique environ 45 000 tonnes de laine de verre par an sous forme de panneaux et rouleaux pour l’isolation des toitures et un produit à base de fibres qui peut être injecté dans les murs creux ou soufflé dans les combles.
Elle abrite trois lignes de production de laine de verre, ainsi qu’une quatrième qui fabrique le matériau en fibre de verre servant de revêtement à certains de ses produits. Bas Beishuizen est ingénieur de la maintenance sur le site. Sa mission est de veiller à ce que les équipements de ces lignes fonctionnent en toute fiabilité et efficacité.
La production de laine de verre étant une activité à grande vitesse, à grands volumes et très énergivore, l’équipe de maintenance doit veiller sur de nombreuses machines. « L’ensemble du site compte 57 équipements stratégiques. Ce sont principalement des pompes et des ventilateurs, assez volumineux dans certains cas. Nos plus gros ventilateurs sont alimentés par des moteurs de 500 kilowatts, par exemple. »
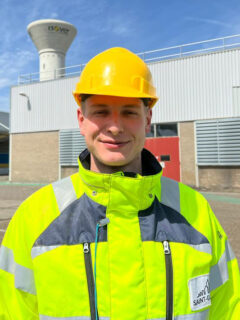
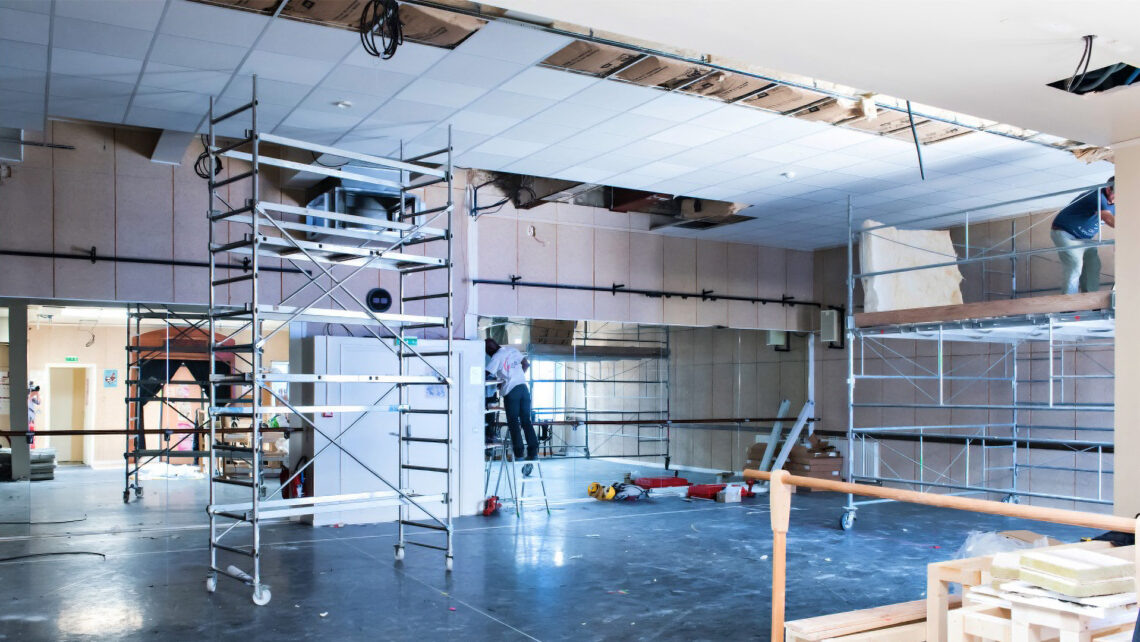
Prévenir l’imprévu
La défaillance d’un outil de production stratégique peut entraîner l’arrêt d’une ligne, voire la mise au rebut d’un lot de production entier. L’équipe de maintenance d’Etten-Leur s’efforce de mettre en place une approche de maintenance préventive conditionnelle chaque fois que c’est possible. « Dans un premier temps, nous avons recours à des capteurs SKF Quick Collect portatifs de détection des vibrations afin d’optimiser la maintenance des roulements. Nous déterminons la fréquence du relevé des mesures des vibrations en fonction de l’importance et de la criticité du composant. Un technicien effectue les mesures, puis les roulements sont analysés en collaboration avec SKF. Ces données nous indiquent l’éventuelle présence de problèmes. »
Grâce à l’aide des experts en maintenance conditionnelle de SKF, l’outil portatif a rapidement fourni des informations utiles.
Bas Beishuizen, ingénieur de maintenance chez Saint-Gobain Isover
Grâce à l’aide des experts en maintenance conditionnelle de SKF, l’outil portatif a rapidement fourni des informations utiles. L’analyse des spectres de vibrations a montré, par exemple, que certains roulements n’étaient pas suffisamment lubrifiés. « Quand on a approfondi la question, on a découvert que les points de lubrification de certaines machines étaient mal positionnés : la graisse n’arrivait pas au bon endroit à l’intérieur du roulement. Une fois la cause connue, il a été facile de trouver un remède. »
Les mesures de vibrations ne révèlent pas uniquement des problèmes attenant aux roulements. Elles peuvent également détecter des anomalies sur la même machine. « Un problème courant chez Saint-Gobain Isover est le balourd observé sur les ventilateurs. Les impuretés peuvent s’accumuler sur les pales de leur hélice, ce qui leur fait perdre de l’efficacité et peut entraîner une panne. »
« Les mesures de vibrations permettent à l’équipe de maintenance de travailler avec l’équipe d’exploitation pour nettoyer les ventilateurs sales et procéder à leur équilibrage pendant un arrêt programmé. Cela réduit les pannes provoquées par la défaillance des roulements ou celle des fixations du moteur dues aux fortes vibrations. »
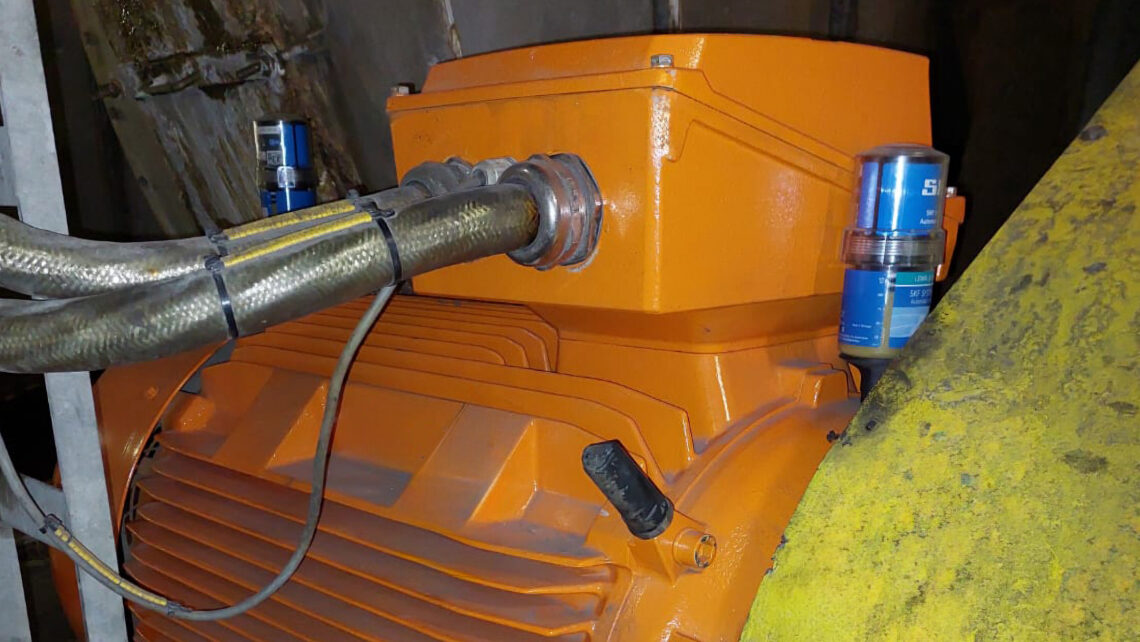
Surveillance en ligne
Encouragé par les bons résultats des mesures de vibrations, Bas Beishuizen souhaitait aller plus loin dans cette démarche. « Les mesures manuelles permettent d’obtenir des données très utiles, mais elles ne sont effectuées qu’un certain nombre de fois par an. L’équipe de maintenance veut disposer de plus de données. Il nous faut donc des mesures plus régulières pour obtenir et accumuler des données de qualité. »
Pour ce faire, elle a opté pour une technologie de surveillance en ligne. Elle a installé des capteurs fixes SKF IMx-1 sur les machines stratégiques à travers tout le site. Ces appareils compacts, alimentés par batterie, enregistrent en permanence les vibrations et la température et transmettent ces informations via un réseau radio maillé sans fil à une passerelle, laquelle les envoie au Cloud SKF via une connexion mobile 4G. « Chez Saint-Gobain, nous disposons déjà de notre propre plateforme logicielle de gestion de la maintenance. Grâce à la connexion API entre SKF et Saint-Gobain, nous pouvons extraire toutes les données de vibration et les joindre à toutes nos autres données. Cela nous permet de gérer toutes les données au même endroit. »
La surveillance continue des vibrations présente de multiples avantages potentiels pour l’usine. Si, par exemple, les vibrations augmentent soudainement et de manière inattendue, le système peut avertir l’équipe de maintenance ou d’exploitation pour qu’elle mène l’enquête. L’enregistrement des données dans la durée aidera l’équipe à repérer des tendances plus progressives susceptibles d’indiquer un début de dégradation des performances d’une machine.
« L’équipe de maintenance est en train de concevoir un tableau de bord de surveillance des équipements afin de mettre en place une véritable maintenance conditionnelle à l’usine Isover. Le tableau de bord nous donne une vue d’ensemble de tous nos outils de production stratégiques et priorise les machines qui nécessitent une attention particulière. »
« Nous arrêtons chaque ligne plusieurs fois par an pour des opérations de maintenance planifiée. Nous aimerions en arriver au point où, grâce aux données, nous déterminerons avec exactitude les interventions nécessaires à chaque fois. »
Ceci permettrait d’améliorer la maintenance et de raccourcir les arrêts ; les inspections avant les arrêts sont déjà effectuées via les analyses.
Mais ce n’est que la prochaine étape, affirme Bas Beishuizen. L’équipe de maintenance a bien d’autres projets ambitieux liés à la digitalisation de la maintenance dans l’usine. « En associant les données d’état aux données d’exploitation et de maintenance, on peut dresser un tableau plus complet des performances de nos outils de production stratégiques, ainsi que de la manière dont ils tombent en panne et le moment où cela se produit. Ceci nous permettra de concentrer nos efforts sur des projets qui améliorent la fiabilité et l’efficacité de nos opérations. »
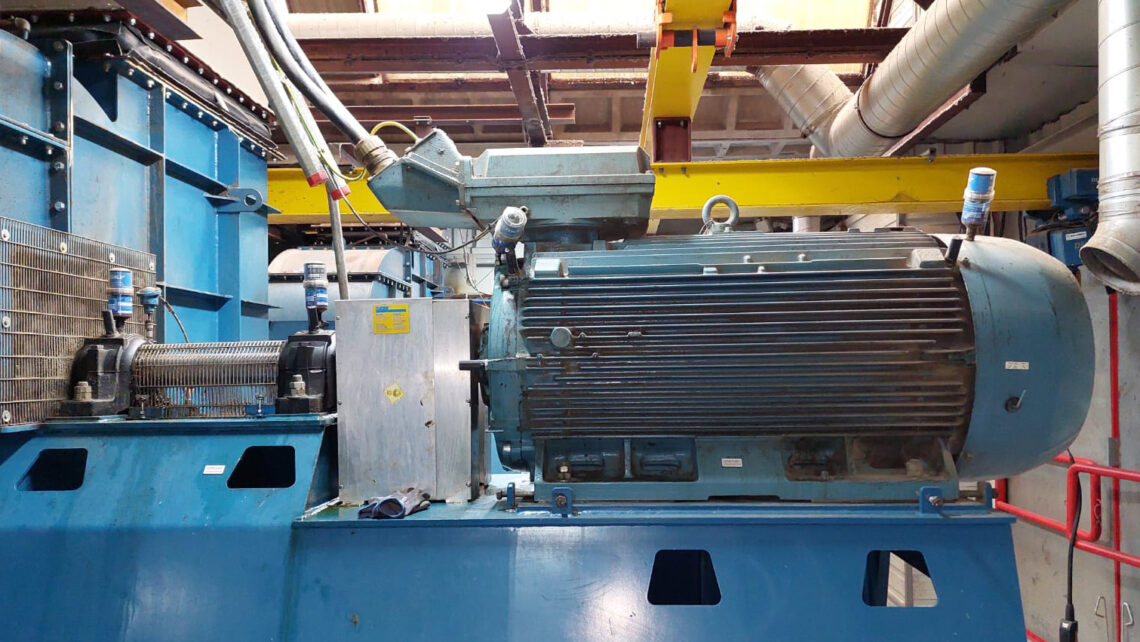
Fabrication par action centrifuge
La production de laine de verre ressemble un peu à la confection de la barbe à papa dans les fêtes foraines où une machine transforme le sucre fondu en nuage duveteux. Ici, cependant, les processus dégagent nettement plus de chaleur et l’opération se déroule à une tout autre échelle.
Tout d’abord, des quantités précises de matériaux sont mélangés, puis enfournées à environ 1 400 ºC. Par le passé, ces matériaux étaient les ingrédients de base du verre : du sable, du carbonate de soude et du calcaire. Aujourd’hui, près de la moitié du mélange introduit dans les fours Isover est du verre recyclé. Ceci permet de réduire la consommation de ressources naturelles et d’économiser de l’énergie pendant la production, car le verre fond à une température plus basse que le sable.
Le verre liquide passe ensuite dans des assiettes de fibrage, qui le transforment par centrifugation en fibres très fines ressemblant à des cheveux. Un liant est pulvérisé sur ces fibres qui sont façonnées en matelas. Ceux-ci passent dans une étuve de polymérisation, où ils sont comprimés jusqu’à l’obtention de leur épaisseur finale. Le liant durci maintient en place les fibres là où elles se croisent, créant un matériau durable qui peut être réduit à un dixième de son volume pour le transport (il reprend son volume d’origine une fois déballé). En fonction de l’application finale, un revêtement en fibre de verre peut être collé sur les matelas pour améliorer encore leur durabilité et leur manipulation.
La dose idéale
delubrifiant
Après avoir constaté l’impact des défaillances de lubrification sur les outils de production stratégiques, l’usine d’Etten-Leur a adopté une autre technologie SKF sur un grand nombre de ses machines. « Nous savons qu’un roulement peut nécessiter 50 g de graisse pour six mois de fonctionnement, explique Bas Beishuizen, ingénieur de maintenance chez Saint-Gobain Isover. Mais on n’obtient pas les meilleures performances si on injecte la totalité du lubrifiant en une seule fois ; en outre, il n’est pas toujours évident de savoir si le roulement est réellement lubrifié. »
À la place, l’usine a installé des graisseurs monopoints connectés SKF TLDD. Ces dispositifs injectent à un rythme prédéterminé de petites doses de graisse à chaque roulement à partir d’une cartouche remplaçable. Ils envoient un rapport sur leur état au Cloud SKF via un réseau sans fil et une passerelle informatique vers le réseau mobile 4G. Ainsi, l’équipe de maintenance sait si les roulements ont été graissés, à quel moment la cartouche doit être remplacée et si un problème a interrompu la distribution de graisse.