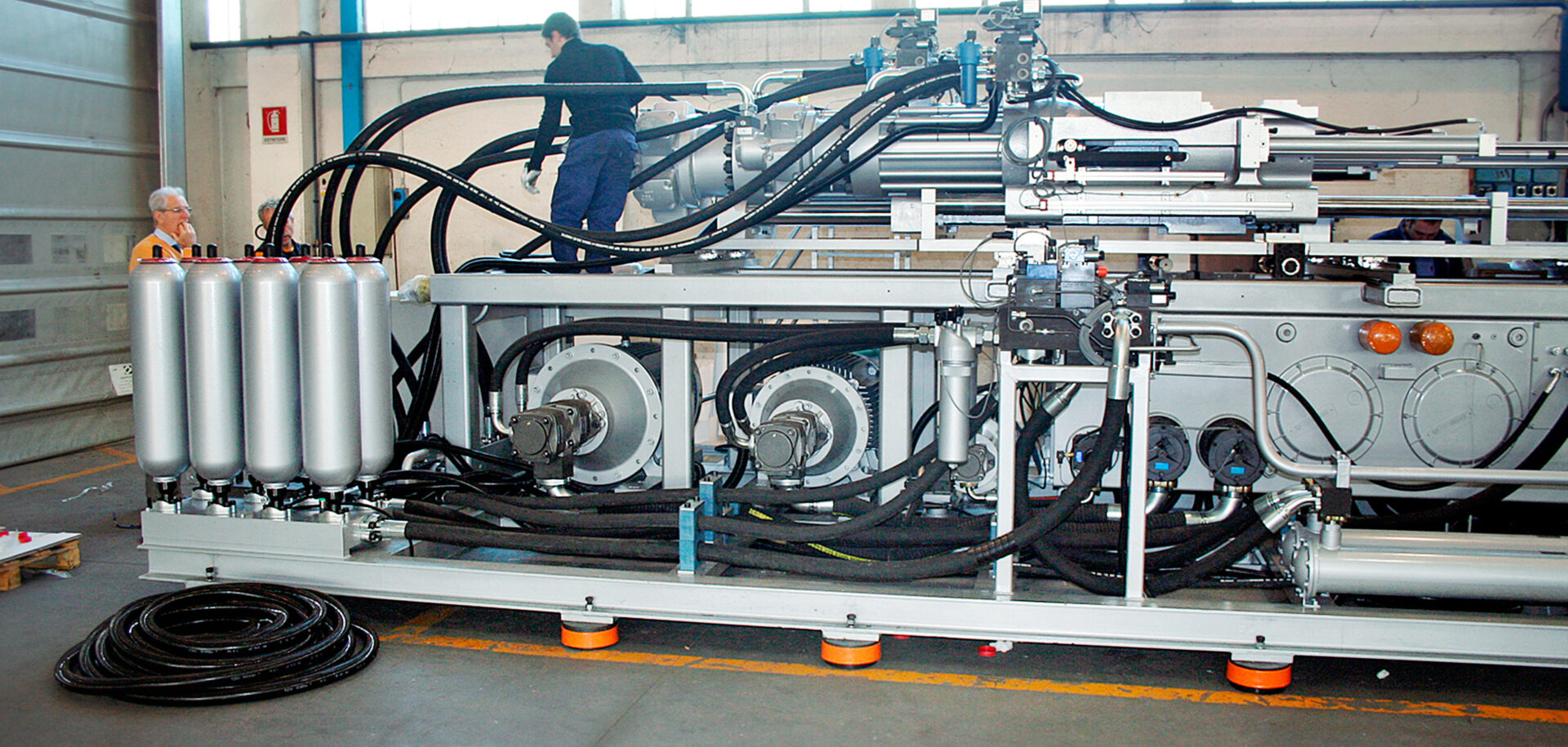
Plastique électrisant
Une entreprise familiale italienne est en train de modeler l’avenir de la technologie du moulage par injection.
En bref
BMB SPA
- Création : en 1967 à Brescia, en Italie.
- Direction : Egidio Bugatti, PDG ; Marco Bugatti, directeur général.
- Implantation : siège à Brescia ; agences commerciales dans 30 pays.
- Entreprise privée.
- Gamme : machines à injecter (hybrides, électriques et hydrauliques).
- Chiffre d’affaires : 70 millions d’euros en 2011.
- Effectif : 180 salariés dans le monde entier.
Liens apparentés
Contact commercial
Giuseppe Saroglia, giuseppe.saroglia@skf.com
En 1967, l’avenir, c’était le plastique à en croire le film Le lauréat. Cette année-là, trois Italiens de Brescia, près de Milan, fondent tous leurs espoirs sur cette assertion et créent l’entreprise BMB, initiales de leurs patronymes : les frères Bugatti, Egidio et Domenico, et Moreschi Giuseppe, leur beau-frère. Ils se lancent dans la fabrication de presses à injecter.
Egidio compte déjà plus d’une dizaine d’années d’expérience dans ce domaine et dans l’étude de la géométrie des embiellages. Les trois partenaires sont convaincus que l’industrie du plastique ne peut que se développer et qu’ils feront de même en concevant des machines plus performantes, plus précises et plus fiables que celles de leurs concurrents. « Il nous fallait faire mieux », se souvient-il, car la concurrence est alors féroce.
En partant de ce principe, la jeune entreprise parvient à décrocher des commandes de multinationales très en vue telles que Olivetti, Bic et Coster, des clients prestigieux dont les produits exigent de la rapidité, de la précision et un contrôle qualité intégré. « Ils ont contribué à notre croissance et nous ont permis de nous positionner sur le segment haut de gamme du marché. »
BMB se développe dans les années 1970 en mettant l’accent sur trois grands principes : qualité, précision et intégrité vis-à-vis des clients. Elle dépose son premier brevet en 1980 et devient le premier fabricant de machines à injecter à intégrer de l’électronique dans ses produits.
En 1980 toujours, ses locaux ne sont plus assez grands pour accueillir son activité. Elle emménage alors là où se trouve actuellement son siège, en périphérie de Brescia, dans la principale zone industrielle. À l’heure actuelle, on dénombre trois bâtiments contigus qui accueillent les services administratifs, les services techniques et trois espaces de production (pour les machines inférieures à 400 tonnes, de 450 à 3 500 tonnes, et supérieures à 3 500 tonnes). D’une superficie de 30 000 m2, l’ensemble du site est on ne peut plus moderne et méticuleusement entretenu.
L’expansion de BMB se poursuit dans les années 1980. Elle produit des machines à injecter traditionnelles hautes performances et haute fiabilité. Si elle parvient à vendre quelques machines à l’étranger, son marché et sa réputation restent pratiquement limités à l’Italie.
Tout commence à changer au début des années 1990. Diplômé de l’école polytechnique de Milan, le fils d’Egidio, Marco Bugatti, rejoint les cadres en 1994 après avoir travaillé quelque temps pour BMB au Royaume-Uni. Il insiste pour modifier la structure commerciale de l’entreprise et accorder plus d’importance aux marchés étrangers. Actuellement, 85 % du chiffre d’affaires de BMB est réalisé hors d’Italie, avec une forte demande en provenance d’Amérique latine et une récente incursion en Amérique du Nord.
Encore plus spectaculaire est le changement intervenu dans la gamme de produits. Il y a encore huit ans, toutes les machines à injecter de BMB étaient hydrauliques. Désormais, elles ne sont plus que 20 %. Conçues par BMB en 2005, les machines entièrement électriques représentent 35 à 40 % de la production annuelle tandis que les machines hybrides, lancées en 2007, complètent la gamme.
Les machines à injecter électriques sont utilisées au Japon depuis 1983. Néanmoins, en dépit de leurs atouts (économie d’énergie, précision, respect de l’environnement, relative compacité et coût moins élevé tout au long de la durée de vie), elles sont beaucoup plus onéreuses à l’achat. En dehors du Japon, peu d’acheteurs sont disposés à les essayer. Ils changent d’avis quand les cours de l’énergie montent en flèche : une machine électrique est certes 30 à 40 % plus chère au départ, mais elle permet d’économiser 40 % des coûts engendrés pendant le cycle de vie – en plus de ses autres avantages.
BMB réalise son premier prototype électrique en 2002 et se diversifie dans les hybrides lorsque ses clients lui demandent des machines plus grandes, capables d’atteindre des vitesses plus
élevées pour les produits fragiles et aux parois fines que les machines électriques ne peuvent pas encore traiter. Par exemple, son hybride eKW70PI/7000, lancée en 2008, fabrique des pots de yaourt avec un moule 16 + 16. Elle est électrique pour toutes les fonctions à l’exception de l’injection de plastique, laquelle est entraînée par un système à accumulateurs hydrauliques afin d’atteindre les vitesses de remplissage nécessaires.
Egidio et Marco Bugatti sont tous les deux convaincus que demain, leur industrie sera 100 % électrique : « Il y a de fortes perspectives de croissance dans le secteur du moulage par injection, estime Bugatti senior. Et nous avons l’intention de rester à l’avant-garde de son développement. »
Un géant de l’électromécanique
Lorsque BMB commence à se spécialiser dans les machines électriques en 2004, elle fait appel à SKF. « Nous savions que SKF avait le savoir-faire nécessaire dans le domaine des vis à rouleaux et des machines à injecter électriques, explique Egidio Bugatti, PDG de BMB. Nous voulions collaborer afin de mettre au point une machine électrique capable d’effectuer un cycle de quatre secondes à grande vitesse. »
La gamme SKF de vis à rouleaux satellites à très haute capacité de charge a été créée spécifiquement pour relever ce type de défi. Exemple avec la nouvelle machine hybride à injecter BMB de 1 700 tonnes : son embiellage est le plus grand jamais fabriqué avec une technologie électromécanique. Les pressions nécessaires sont si élevées qu’elles entraînent un risque de défaut d’alignement. Les vis à rouleaux satellites SKF sont conçues spécialement pour éviter ce genre de problème et les arrêts machine qui en découlent. En outre, ajoute Giuseppe Saroglia, responsable commercial mécatronique chez SKF, « elles réduisent considérablement le volume de fluide hydraulique nécessaire et le besoin de refroidissement de celui-ci. »