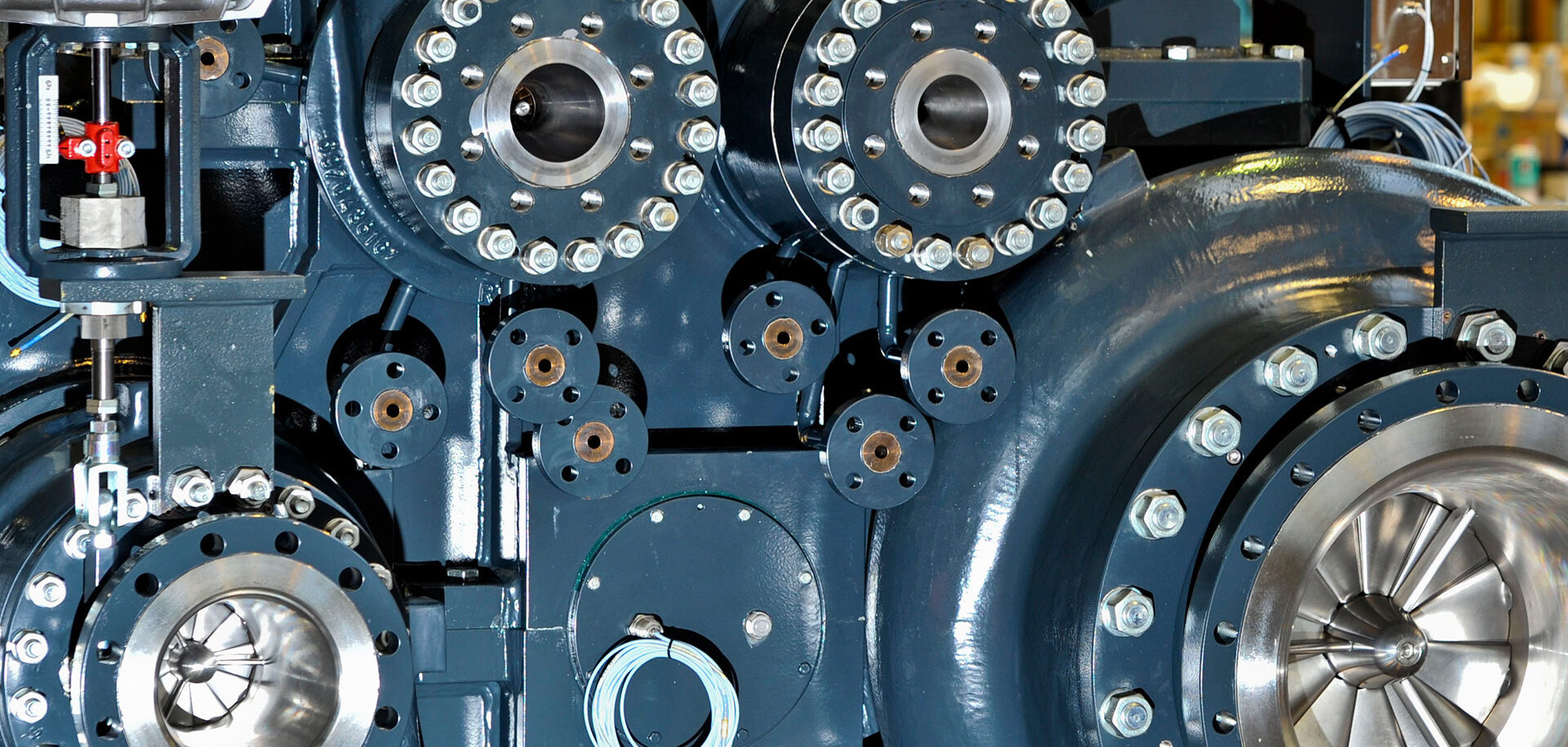
Des économies d’énergie grâce à des solutions de roulements plus efficaces en remplacement des paliers lisses hydrodynamiques
Les solutions et la puissance de l’ingénierie de SKF facilitent la transition des paliers lisses hydrodynamiques vers des systèmes de roulements plus efficaces.
La question, ô combien importante, de l’utilisation optimale des ressources et de l’énergie, notamment dans l’industrie et le secteur de la production électrique, est plus que jamais à l’ordre du jour au niveau mondial. Malgré les progrès technologiques, une quantité d’énergie importante est dilapidée partout dans le monde dans des frottements mécaniques et des pertes hydrodynamiques de machines tournantes : compresseurs, turbines, ventilateurs et pompes notamment. Cet article fournit des explications illustrées par des exemples concrets concernant les économies considérables sur l’énergie et sur les coûts permises par des roulements à éléments roulants modernes en remplacement des paliers lisses hydrodynamiques.
Il n’est pas rare que des équipements industriels, comme les pompes, les compresseurs et les soufflantes, soient sollicités entre 4 000 et 8 000 heures par an, ce qui explique la part écrasante de l’énergie électrique dans le coût du cycle de vie (CCV) et dans les émissions de ces équipements. Dans de nombreux cas, les entraînements à vitesse variable (VSD) constituent un moyen très efficace d’améliorer le rendement énergétique. La conception du système roue-roulements-étanchéités est également déterminante et ces éléments doivent être choisis avec soin.
Depuis des millénaires, l’humanité utilise des éléments roulants (barres, rouleaux, billes) pour réduire le frottement et l’échauffement dans les machines tournantes et de transport, et obtenir un positionnement précis et fiable des arbres tournants. C’est ce qui vaut aux roulements à éléments roulants d’être parfois qualifiés de composants anti-frottement ou de précision. Cependant, pour différentes raisons techniques et historiques, de nombreux paliers « à frottement », appelés généralement paliers lisses, à glissement, à film fluide ou à patins oscillants, ou plus spécifiquement paliers hydrodynamiques ou hydrostatiques, sont encore utilisés dans le monde.
Roulements à éléments roulants versus paliers lisses hydrodynamiques
Les paliers hydrodynamiques mettent à profit les principes de la lubrification hydrodynamique connus de longue date : la surface en acier de l’arbre tournant est séparée de sa surface d’appui fixe par un film fluide (huile). Correctement lubrifiés, des paliers hydrodynamiques ne présentent pratiquement aucune fatigue ou usure mécanique, et le film fluide exerce une meilleure atténuation des contraintes par rapport aux roulements à billes et à rouleaux. Grâce au film d’huile relativement épais, la contamination a moins d’impact sur leurs performances, car les particules dures sont en partie incorporées dans le manchon plus tendre ou dans des matériaux amortisseurs, ce qui évite les dommages causés aux surfaces de contact.
Cependant, les paliers hydrodynamiques présentent des jeux relativement importants et sont soumis à l’usure et l’abrasion en cas d’arrêts-redémarrages fréquents ou à des vitesses très faibles, comme c’est le cas dans les applications à entraînement à SFV. En cas de faible viscosité de l’huile lubrifiante ou de dilution dans le fluide du process, la formation d’un film d’épaisseur suffisante peut ne plus être assurée. Les performances des paliers hydrodynamiques, en particulier des butées à patins oscillants, sont alors compromises. Dans ce cas, les roulements à éléments roulants, a fortiori lorsque ces derniers sont en céramique, constituent une bonne alternative, car ils peuvent fonctionner avec des lubrifiants de viscosité inférieure ou dilués.
De même, les roulements à éléments roulants offrent souvent la meilleure solution en cas de fonctionnement intermittent et d’environnement froid en raison de leur faible frottement de démarrage. Cela vaut particulièrement pour les roulements hybrides dotés d’éléments roulants en céramique. Plus important encore du point de vue du rendement énergétique : le frottement en fonctionnement des roulements à éléments roulants est généralement nettement inférieur, au moins à des vitesses faibles et modérées. Selon J/E Bearing & Machine Ltd [1], le film lubrifiant idéal dans les paliers lisses hydrodynamiques nécessite jusqu’à trois fois plus d’énergie pour fonctionner, même sans tenir compte des pertes au démarrage. La représentation schématique ci-dessous illustre un résultat typique de comparaison des pertes (de puissance) par frottement dans les paliers lisses par rapport aux roulements à billes ou à rouleaux.
La solution gagnante : les roulements à éléments roulants dans les turbocompresseurs et vilebrequins
Comme tous les ingénieurs et les passionnés de voitures puissantes le savent, les turbocompresseurs à roulements à billes dominent sur la scène du sport automobile depuis l’apparition des premiers roulements de ce type en remplacement des paliers lisses aux 24 heures du Mans dans les années 1990. Deux raisons principales ont motivé ce changement. Tout d’abord, le frottement de fonctionnement des systèmes de roulements à billes s’est révélé plus faible. En deuxièmement lieu, ces systèmes évitaient l’utilisation des pompes à huile haute pression qui génèrent des pertes de puissance dans les systèmes à paliers lisses où des quantités importantes d’huile doivent être pompées à travers les minces trous des manchons du tourillon. Des conceptions récentes reposent sur des roulements-cartouches compacts hybrides avec billes en céramique pour des performances encore plus élevées.
Des économies substantielles dans le secteur de la production d’électricité verte
Une centrale géothermique de 250 MW récemment construite en Asie utilise la technologie du cycle organique de Rankine (ORC) pour produire de l’électricité verte à partir de la géothermie. Près de 200 détendeurs à vis y sont utilisés pour actionner les génératrices. Les détendeurs à vis reposent sur le même principe mécanique que les compresseurs à double vis, mais fonctionnent dans le sens opposé pour produire de l’énergie à partir de vapeur détendue, à l’instar d’une turbine à vapeur. Les objectifs de rendement fixés par le propriétaire de l’usine constituaient un véritable défi technique. Les premiers tests ont montré qu’ils ne pourraient pas être atteints avec des paliers hydrodynamiques. Il faut savoir que dans les gros détendeurs à vis, les paliers hydrodynamiques sont au nombre de cinq ou six.
Les ingénieurs SKF ont donc entrepris une modification des détendeurs destinée à permettre l’utilisation de roulements à rouleaux. Parallèlement au frottement réduit, les tolérances serrées des roulements à éléments roulants permettent aux machines à vis de fonctionner avec des jeux d’extrémité très étroits entre les axes des vis et le logement, ce qui augmente encore l’efficacité. Des calculs et des tests ont montré que les pertes d’énergie associées pouvaient être considérablement réduites et passer de 30 kW à 12 kW. Autrement dit, pour un seul détendeur, la production électrique pouvait être augmentée de 18 kW en recourant à un système de roulements à éléments roulants.
Une réduction des pertes de puissance de 18 kW peut se traduire par une production d’électricité supplémentaire de 100 000 kWh – par machine et par an. Compte tenu du grand nombre de détendeurs à vis installés dans une seule usine, l’augmentation des revenus annuels peut atteindre plus d’un million de dollars.
Refroidisseurs et pompes à chaleur industriels
Les gros refroidisseurs ou pompes à chaleur commerciaux ou industriels font généralement appel à des compresseurs centrifuges ou alternatifs pour comprimer un gaz réfrigérant destiné à transférer la chaleur d’une source à basse température vers un dissipateur à température plus élevée. De nombreux compresseurs frigorifiques intégraient traditionnellement ou intègrent encore des boîtes d’engrenages comprenant souvent des paliers hydrodynamiques lubrifiés avec un mélange huile-fluide réfrigérant.
L’introduction de nouveaux fluides réfrigérants plus respectueux de l’environnement (par exemple, les hydrofluoro-oléfines [HFO] à faible potentiel de réchauffement planétaire et d’appauvrissement de la couche d’ozone) et les niveaux de température nettement supérieurs requis pour les pompes à chaleur ou les refroidisseurs de data centers ont un effet néfaste : le taux de dilution de l’huile par les fluides réfrigérants augmente, jusqu’à atteindre parfois les 50 % ou plus. Dans certains cas, la viscosité de l’huile devient alors insuffisante pour les paliers hydrodynamiques des compresseurs. Ils sont alors remplacés par des roulements à éléments roulants qui offrent comme avantages supplémentaires des pertes par frottement réduites et une précision de position de la roue accrue.
En collaboration avec des spécialistes des applications et des clients importants, nous avons recueilli des données sur les pertes par frottement issues d’essais et de l’expérience sur le terrain. La Figure 3 présente des données relatives à un refroidisseur centrifuge de taille moyenne (~300 kW). Cette comparaison porte sur les types de pertes suivants : frottement des paliers ou roulements, pertes volumétriques au niveau des passages d’étanchéité, pertes des clapets anti-retour et pertes de transfert de chaleur dues à la contamination des échangeurs thermiques par de l’huile mêlée au gaz réfrigérant.
Ces données montrent que les roulements à éléments roulants génèrent moins de pertes par frottement, mais aussi moins de pertes volumétriques au niveau des passages d’étanchéité grâce à une plus grande précision de fonctionnement. Autre effet positif sur l’efficacité, la lubrification des roulements à rouleaux nécessite beaucoup moins d’huile (moins de 10 % généralement) que celle des paliers hydrodynamiques. Il y a donc moins d’huile mélangée au réfrigérant, d’où une moindre contamination de l’huile dans les échangeurs de chaleur. Il est ainsi possible d’accroître le rendement du refroidisseur de 3 à 4 % en utilisant des roulements à éléments roulants lubrifiés à l’huile à la place de paliers hydrodynamiques. Une autre étape importante dans l’amélioration de l’efficacité peut être franchie en concevant des refroidisseurs sans huile, basés soit sur des paliers magnétiques SKF, soit sur des solutions de roulements PRL (lubrifiés uniquement par le réfrigérant) SKF, comme indiqué dans la brochure Evolving Chiller Performance de SKF et dans cet article d’Evolution.
Gros compresseur à vis d’ammoniac
Récemment, SKF a joué un rôle important dans la conception d’une nouvelle génération de compresseurs à vis d’ammoniac de grande taille pour des applications de refroidissement et de réfrigération. Le client, leader dans son domaine, avait pour habitude d’utiliser des paliers hydrodynamiques montés avec un jeu relativement important pour la reprise des charges radiales et des roulements à billes à contact oblique pour les charges axiales. Aujourd’hui, des roulements à rouleaux cylindriques avec des tolérances de jeu radial serrées offrent une alternative aux paliers hydrodynamiques. Cette solution améliore le rendement volumétrique du compresseur et peut également se traduire par une réduction de la consommation d’huile du système du compresseur.
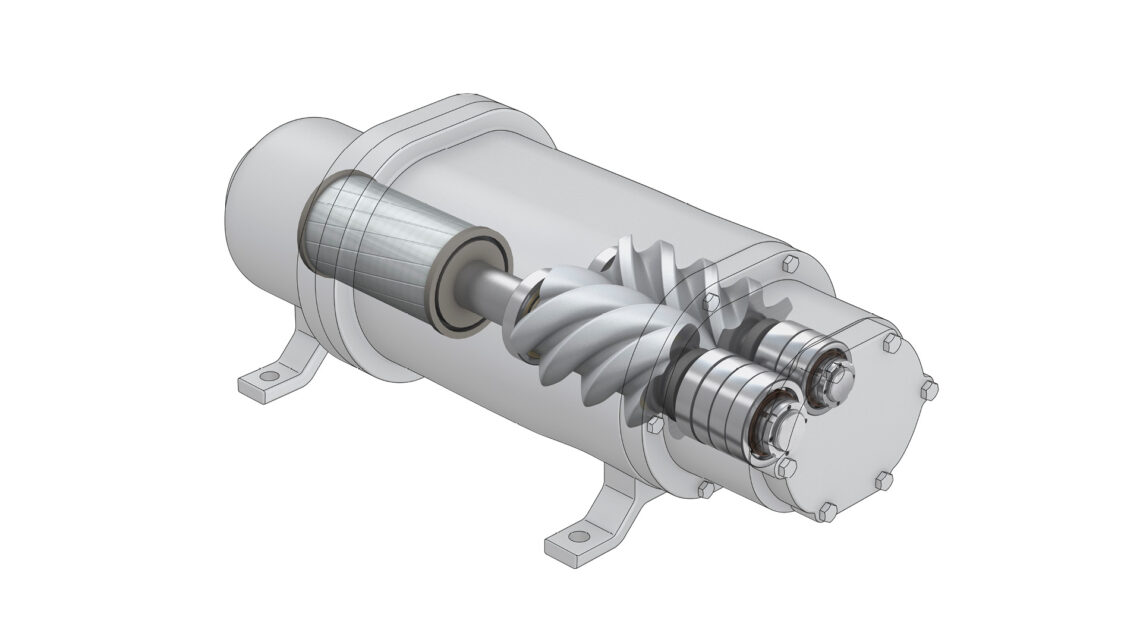
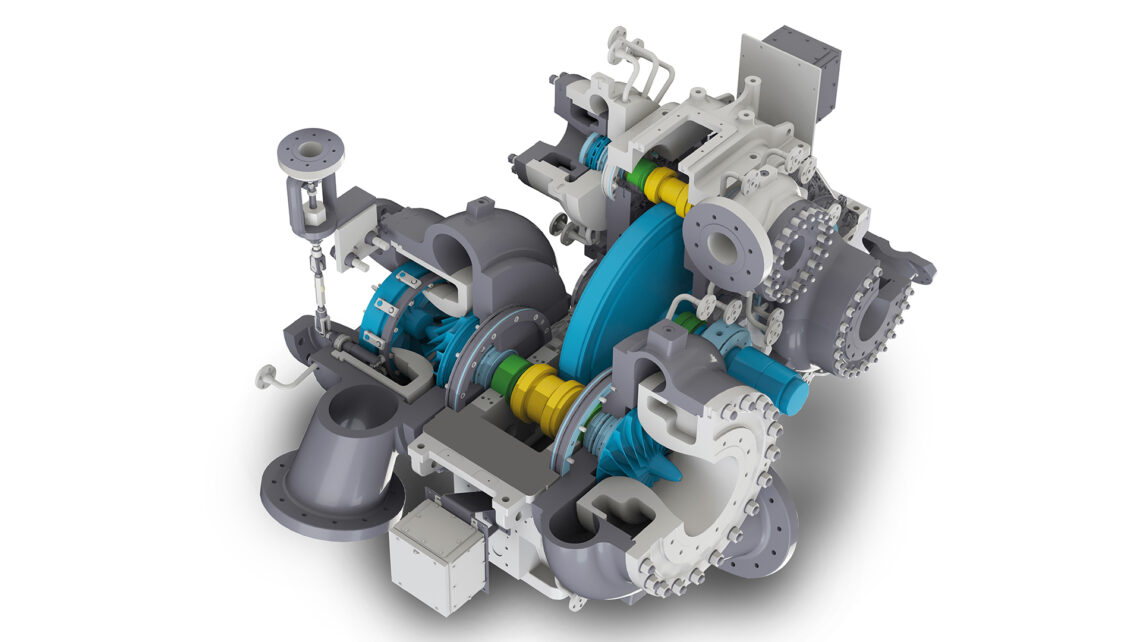
Cette image et la photo au début de l'article sont reproduites avec l'aimable autorisation d'Atlas Copco Gas and Process.
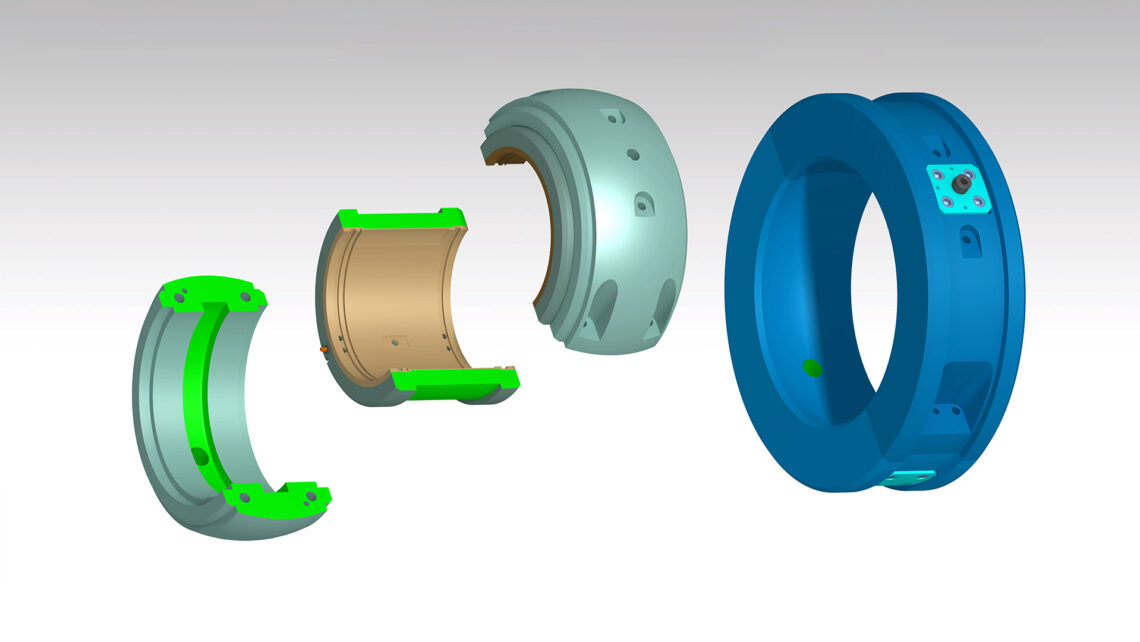
Avantages des roulements à éléments roulants par rapport aux paliers hydrodynamiques :
- précision de positionnement élevée autorisant des passages plus étroits pour les joints et les roues, ce qui réduit les pertes de débit (pertes volumétriques) ;
- frottement de fonctionnement réduit ;
- plus adaptés aux arrêts-redémarrages fréquents ou aux vitesses très faibles (variateurs de vitesse par ex.) ;
- supportent une faible viscosité et une dilution élevée de l’huile ;
- réduction de 90 % des volumes d’huile lubrifiante requis et diminution des besoins de maintenance du système d’huile ;
- réduction de la complexité et du coût de l’ensemble du système ;
- montages de roulements plus simples pour des charges axiales et combinées ou pour des défauts d’alignement importants.
[1] J/E Bearing & Machine Ltd., “Plain or Rolling Bearings – Which is Best?”
[2] Vanhaelst R, Kheir A, Czajka J, “A Systematic Analysis of the Friction Losses on Bearings of Modern Turbocharger”, Combustion Engines 1/2016 (164), pages 22–31.
[3] Morales G. E., Hauleitner R., Wallin H., « Technologie de lubrification des compresseurs centrifuges sans huile basée exclusivement sur le fluide réfrigérant », Evolution 2 mars 2017.