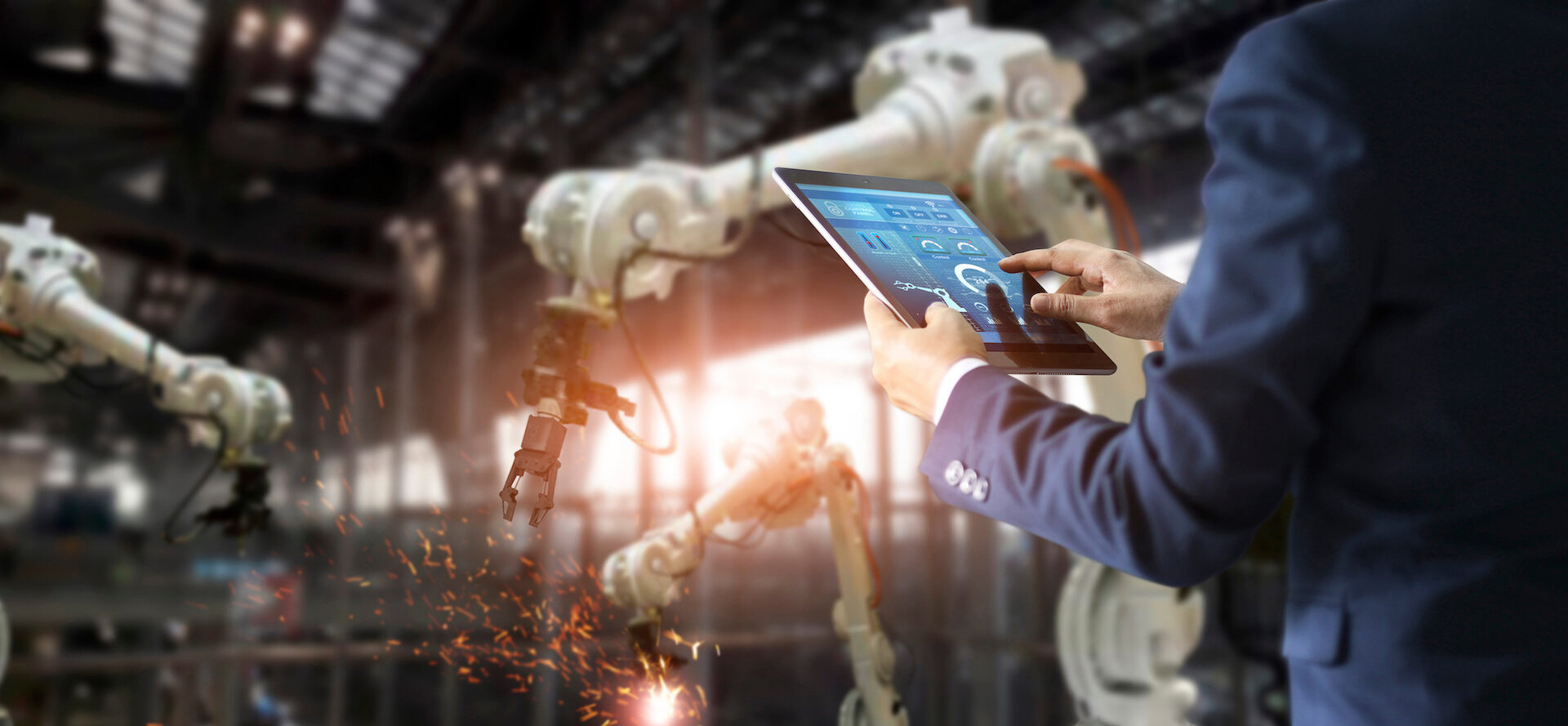
Une greffe qui prend bien
Finies les crises provoquées par la panne des équipements depuis l’installation du machine health reporting program, un service SKF très pointu. Il suffit désormais d’intervenir sur les machines avant leur défaillance.
En bref
RTI Biologics en Floride
RTI Biologics, l’un des premiers fournisseurs mondiaux de greffons biologiques stériles, s’investit dans le progrès scientifique, la sécurité et l’innovation. L’entreprise prépare les dons de tissus bovins et humains pour la transplantation en procédant à des examens et à des tests de dépistage, en les façonnant et en les stérilisant par l’intermédiaire de procédés validés et brevetés. Ces greffons xénographes et allographes servent à la chirurgie touchant la colonne vertébrale, sportive, orthopédique, dentaire et autres.
Finies les crises provoquées par la panne des équipements depuis l’installation du machine health reporting program, un service SKF très pointu. Il suffit désormais d’intervenir sur les machines avant leur défaillance.
Affaires
Printemps 2010 : Johnny Simmons III s’entraîne au base-ball, son sport préféré, avec l’équipe de son lycée. Lanceur, il est à son poste sur le monticule lorsque la balle d’un coéquipier le frappe à la tête, écrasant son orbite gauche et déchirant sa rétine. Il s’écroule en pensant qu’il va se relever avec un bel œil au beurre noir. Mais lorsque ses entraîneurs voient du sang s’écouler de ses yeux, oreilles et narines, ils savent que la blessure est grave. En fait, les médecins diagnostiquent qu’il risque de perdre cet œil et de ne jamais plus rejouer au base-ball. Johnny consulte d’autres praticiens qui lui proposent de reconstruire son orbite à l’aide de greffons d’os et de peau formant une sorte de mastic qui reconstitue la structure abîmée. Johnny retrouve la vue de cet œil et rejoint son poste de lanceur un an plus tard.
Par le plus curieux des hasards, son grand-père, Johnny Simmons, ingénieur fiabilité chez SKF USA, travaille avec RTI Biologics, un fournisseur mondial de greffons tissulaires, qui prépare des ciments osseux semblables à ceux utilisés pour reconstruire l’orbite de son petit-fils : « Aujourd’hui, on ne voit même pas qu’il a eu un problème à l’œil. Et il est de retour sur le terrain. »
Fondée en 1998, RTI a produit plus de deux millions d’allogreffons (tissus humains) et de xénogreffons (tissus d’origine animale) sans déplorer une seule infection consécutive à une allogreffe. L’entreprise a mis au point le procédé BioCleanse® qui permet de stériliser les tissus humains et bovins avant toute intervention chirurgicale. Spin-off de l’université de Floride, elle s’est agrandie et a fait son entrée en Bourse en 2000 avant de fusionner, en 2008, avec la firme allemande Tutogen. À l’heure actuelle, elle occupe un site de 16 250 m2 au Progress Corporate Park d’Alachua, une zone d’activité bucolique dédiée aux biotechnologies et aux sciences du vivant dans un coin tranquille du nord de la Floride.
Grâce à ses produits uniques et à son domaine d’expertise unique en son genre, la compagnie a connu une croissance exponentielle en quelques années d’existence seulement. Aujourd’hui, on la considère comme la société de transfert technologique rapportant le plus en termes de recettes à l’université de Floride dont elle est issue, revenus réinvestis dans la poursuite d’autres recherches.
RTI Biologics emploie 700 salariés dans le monde entier, dont 500 à son siège d’Alachua. Ce site d’une propreté immaculée tourne 24h/24 : ses laboratoires sont continuellement prêts à recevoir des dons de tissus humains, qui sont congelés et mis en quarantaine dès leur arrivée en attendant les résultats des examens et des tests de dépistage qui vérifient s’ils sont aptes à être greffés. Ils sont alors façonnés et stérilisés par l’intermédiaire d’un des procédés de stérilisation brevetés par RTI avant d’être envoyés à des chirurgiens dans le monde entier. Chaque phase du processus et chaque recoin du site doivent répondre à tout moment aux normes de qualité imposées aux dispositifs médicaux et tenir compte de la méthode de production « au plus juste ».
Le directeur des installations Chuck Ratliff est chargé de veiller au respect de ces critères. Lorsqu’il est arrivé il y a six ans, la maintenance était plutôt réactive et suivait un programme de maintenance conditionnelle de base : lorsqu’une machine tombait en panne, on appelait les techniciens à n’importe quelle heure du jour ou de la nuit pour une réparation d’urgence. L’équipe réagissait promptement mais la méthode lui imposait d’avoir à disposition un vaste stock de pièces détachées. En cas de panne, il fallait stopper l’ensemble du système, empêchant les implants de parvenir aux patients jusqu’à ce que la réparation de l’équipement défectueux soit effectuée. L’indice de performance du système était de 80 %. L’équipe technique s’est donc mise en quête d’une procédure de maintenance plus efficace susceptible d’améliorer la fiabilité des équipements.
La recherche d’une solution a mis RTI en contact avec SKF et Johnny Simmons, en poste dans le nord de la Floride. Celui-ci a présenté à Chuck Ratliff et Randy Cannon, spécialiste en chef de la maintenance chez RTI, un nouveau système de détection des vibrations mis au point par SKF qui surpassait de loin les normes en cours dans l’industrie. « RTI a été le premier site américain sélectionné pour ce nouveau programme », indique l’ingénieur fiabilité SKF.
Le SKF machine health reporting program repose sur l’enregistrement des données vibratoires. RTI procède à l’inspection par infrarouge et ultrasons de toutes ses machines une fois par mois. Une fois les données collectées, elles sont envoyées par voie électronique à Johnny Simmons. Celui-ci les analyse pour détecter le moindre signe de dysfonctionnement. Il peut ainsi anticiper les problèmes potentiels, et ses rapports permettent à RTI de les identifier et de les résoudre avant qu’ils atteignent le stade de la panne. L’ ancien système reposait sur une inspection trimestrielle, qui ne facilitait pas l’anticipation des problèmes par l’analyse des données. « S’attendre à ce que quelqu’un prévoit une défaillance trois mois à l’avance, c’est beaucoup demander, estime Randy Cannon. C’était un peu au petit bonheur la chance. »
Aujourd’hui, l’indice de performance des équipements est de 98,7 %, et l’équipe technique prévoit de rester à ce niveau de perfection.
Le passage de la démarche réactive au programme de maintenance prédictive n’a pas été sans heurts pour Chuck Ratliff et son équipe. Ils ont certes cessé de recevoir des appels au beau milieu de la nuit, mais ils n’ont plus l’occasion d’éprouver la satisfaction d’avoir résolu un problème urgent. Si les poussées d’adrénaline se font plus rares, le directeur affirme que ses hommes ont fini par apprécier de pouvoir solutionner les problèmes avant leur apparition et les avantages découlant de la bonne marche permanente des machines.
« On est heureux de bien connaître l’état des machines et d’être prêt à les réparer avant leur panne éventuelle. On va faire atteindre à l’entreprise le top niveau mondial. C’est notre objectif en tant que champions de la maintenance conditionnelle. »
Savoir-faire technique
Grâce à son savoir-faire technique, SKF fournit des solutions pour tout type de machine. Depuis plus d’un siècle, ses solutions de roulements novatrices permettent de faire des économies d’énergie et d’améliorer performances et fiabilité. Sa vaste gamme de produits et de services contribue à la préservation des ressources naturelles et à la protection de l’environnement. Son service de pointe machine health reporting program a permis à RTI Biologics de faire passer de 80 à 98,7 % l’indice de performance de ses équipements.