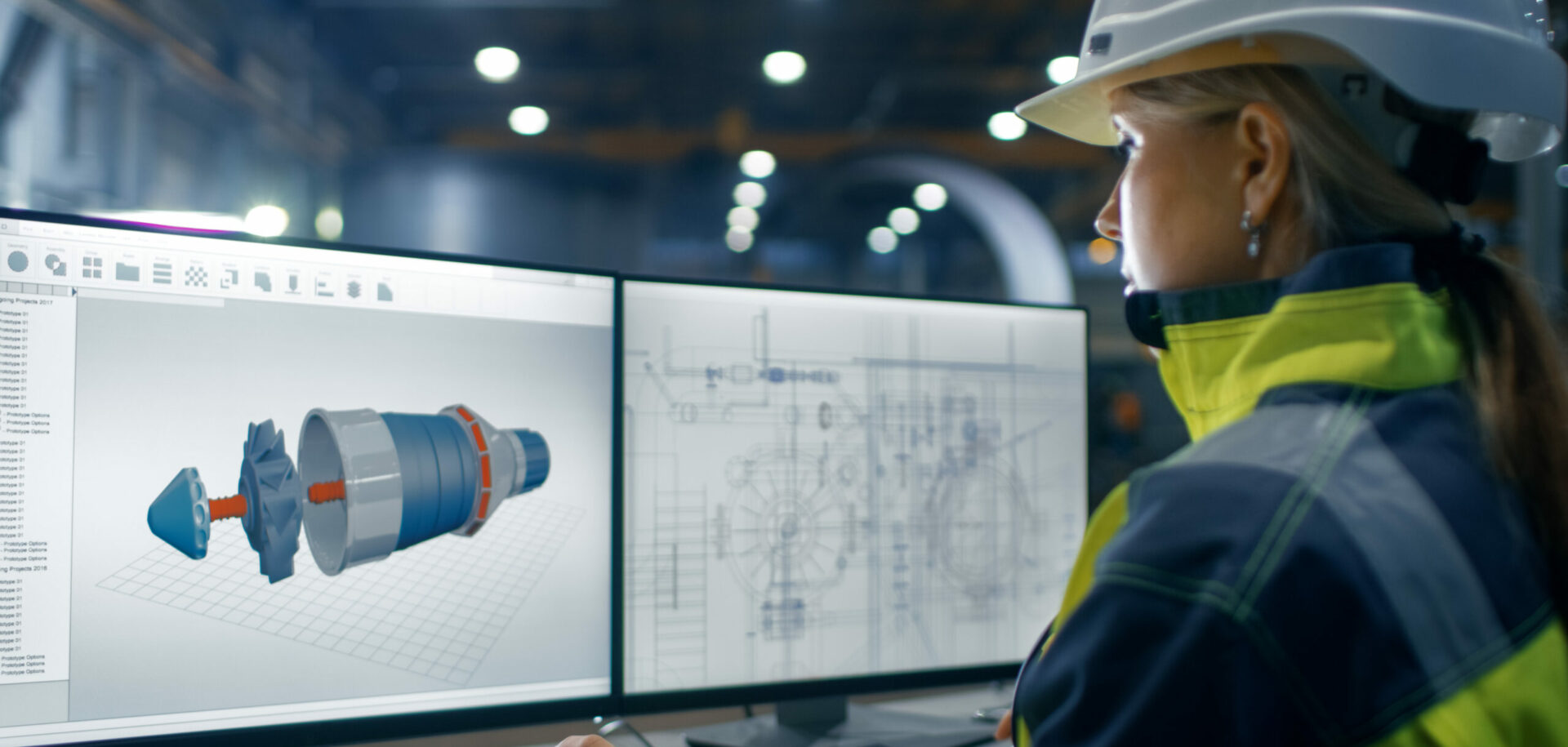
From the racetrack to the streets
While motorsport has long influenced road vehicle design in both aesthetics and performance, the extreme test environment of Formula 1 now plays a critical role in developing fuel-saving technologies for the road.
Since 2009, Formula 1 teams have been shaving a few tenths of a second from their lap times with KERS (kinetic energy recovery system) technology, which recovers the energy generated by braking and uses it to attain higher speeds. This year, the same technology will be fitted to six London buses – not to make them faster, but to reduce their fuel consumption and emissions. While it is common for developments in motorsport to trickle down to mass-production vehicles, the technology transfer has never been so rapid or had such important implications. “In the current economic climate, Formula 1 plays a crucial role in automotive technology development,” says Kirsty Andrew, head of commercial operations at Williams Advanced Engineering, which commercializes the Williams F1 team’s technology. “F1 is good at taking new technologies and rapidly developing them in car racing’s extreme test environment.” On the racetrack, Williams F1 cars get a power boost from a battery version of the KERS system. This technology is spreading to the automotive industry, for example adding power to the Jaguar C-X75 hybrid super-car now under development. But Williams has also developed a flywheel KERS, which has been used on city buses. “It can reduce fuel consumption – and therefore emissions – by recycling the energy generated by the bus’s frequent braking,” says Andrew. “The F1 technology is being used slightly differently, but the basic principles are the same.” Fuel savings may be as high as 20 percent. The trickle-down effect from motorsport to vehicle design happens for both aesthetic and performance reasons. Steve Harper, who designs cars for the road and the racetrack, says that design elements he introduced to enhance performance in motorsport have been incorporated into designs for companies such as Ford and Volvo. “The Ford Escort Cosworth was the first production car with down force front and rear, and we spent a great deal of time in the wind tunnel perfecting its aerodynamic performance,” he says. “Every production car I’ve designed since has used the knowledge gained on the Cosworth when it comes to designing grilles or air intakes.” In the 1980s, Volvo had a reputation for boxy cars, but today its range is admired for its sleek and sporty lines. Harper traces that development back to Volvo’s involvement in the British Touring Car Championships in the early 1990s. “The guys involved with the touring car team went on to the more sporty Volvo projects, bringing with them the aerodynamic lessons they had learned in motorsport,” he says. Behind the wheel, racing’s influence on consumer cars continues. “Traditionally, you had classic leather and wood interiors,” says Harper. “Now we have aluminium and carbon fibre. Whether it’s the material choice or the paddle gearshift, the idea is to make people feel like they’re Michael Schumacher.” Titan Motorsport and Automotive Engineering straddles the motorsport and automotive worlds, producing metal components for racing cars and high-performance road cars. Titan’s Sales and Marketing Manager Zoe Timbrell says that components for both applications can be made with the same material – and even made to the same design. “With automotive we engineer cost out, and with motor sports we engineer performance in,” she says. As with Williams’ KERS systems, Titan technologies that serve one purpose in racing can serve another in automotive. “In motorsport development is all about going faster,” says Timbrell. “In automotive it’s all about using less fuel. Both results can be achieved with the same solutions.” Clive Temple, who leads the motorsport engineering and management programme at Cranfield University in the UK, points out that most original equipment manufacturers are involved in motorsport for marketing reasons, rather than for R&D purposes. Still, he says that Audi has used its involvement in endurance racing to refine diesel technology for its production cars. “For a long time people associated diesels with taxis and lorries,” he says. “But in recent years Audi has adopted diesel for all its cars, including its luxury and sporty models. There definitely is a marketing side to it, but there is also a technological side in terms of the refinement of the diesel engine and powertrain.” At the same time, Temple notes that motorsport regulations, brought in to raise entertainment value, often restrict technology transfer. “Touring cars are not even fitted with an anti-lock braking system, which most road cars have today,” he says. “F1 is meant to be the pinnacle of motorsport and the drivers are meant to be the best, so they have moved away from driver aids that you and I have for our commute to work.” But in the not too distant future, that commute could be powered by F1-derived technology. Andrew at Williams F1 says the KERS system being tested in buses could be applied to cars too. “The price will have to come down, but it’s certainly possible,” she says. The 2014 Formula 1 season will see a switch to smaller V6 engines fitted with a single turbo and new systems for recovering energy. SKF has a key role to play in helping to develop these technologies, which could be used in road vehicles within just a couple of years. Jean-Sylvain Migliore, manager of the SKF Racing Unit, says, “For HERS [heat recovery energy system] and KERS [kinetic energy recovery system], the bearings are key components due to the very demanding requirements for speed, temperature and lubrication, so we are heavily involved at the system level. A lot of experience will come from this, which SKF can apply to solutions for the automotive industry.” The same goes for a new electrical turbo planned for F1. “With the turbo – even more so than with KERS – there will be a lot of learning to transfer to passenger cars within a short timeframe. It is essential to quickly transfer the technology from the SKF racing team to the entire SKF automotive community.” SKF-engineered solutions can be found on almost every car on the starting grid of a Formula 1 race. There is no better test bench for new solutions, features, materials and lubricants. Jean-Sylvain Migliore is the manager of the SKF Racing Unit. “Our core mission is to transfer motorsport technology to our SKF colleagues developing solutions for automotive and industrial OEMs,” he says. “The extreme conditions of motorsport provide a very fast and efficient way to test new developments. These innovations could be on the road – or used in other industries – within 5 to 10 years.” SKF has been involved in motorsport for nearly a century, providing engineered solutions to teams and racing equipment manufacturers around the world. The Racing Unit has a technical partnership with the Ferrari Formula 1 team that goes back 65 years. The unit is also active in rallying, touring cars, NASCAR and other car racing disciplines.
High-speed technology transferThe ultimate test bench