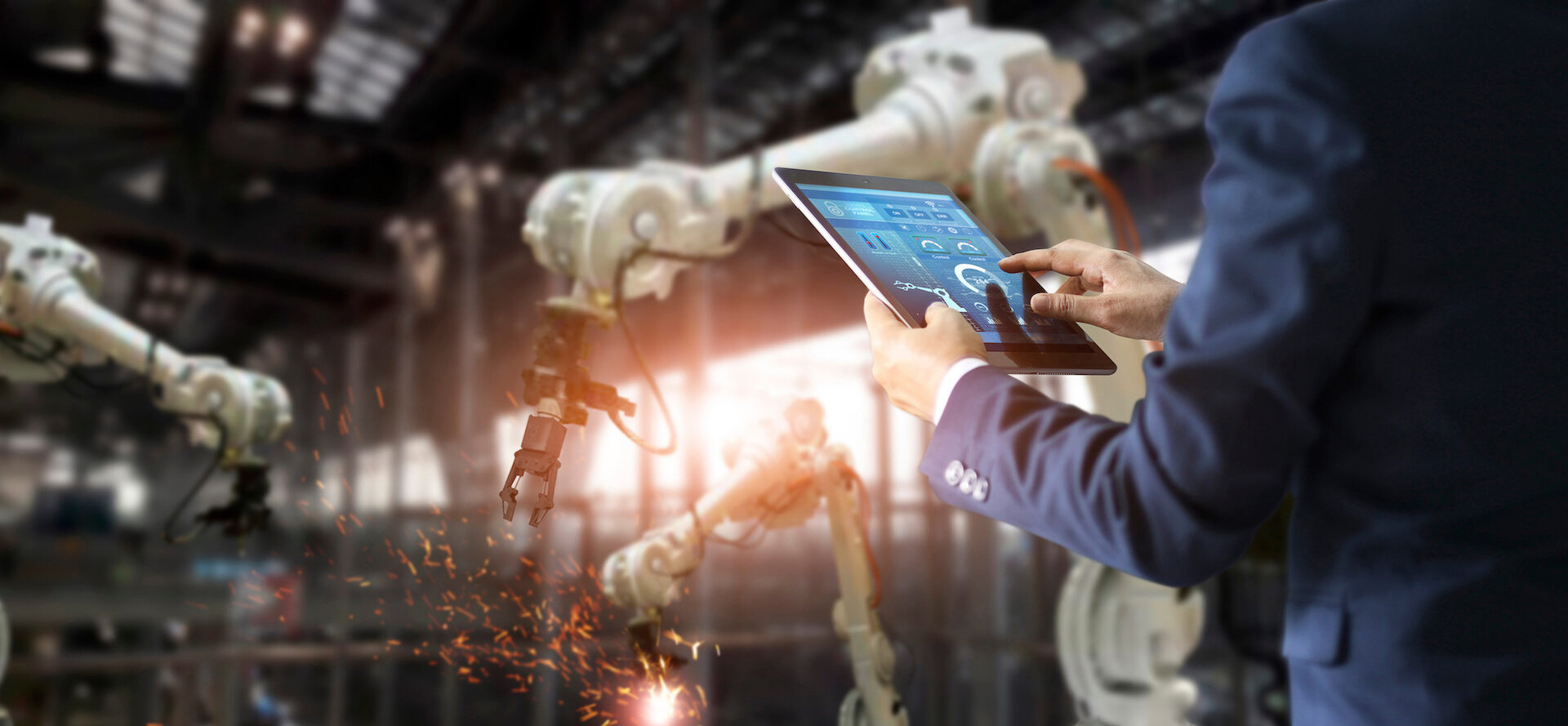
Healthy outlook
Manufacturing is not the only industry that can benefit from taking a closer look at efficiency. In the United States, SKF helped a medical clinic find smarter ways to work, with better care for patients with diabetes a key outcome.
When the Partners in Family Health medical practice in York, Pennsylvania, decided to get serious about improving efficiency, everyone pitched in. Doctors and nurses counted their steps, analyzed patient waiting times and even clocked the speed of their thermometers. As a result of the close scrutiny of working behaviours, the clinic was able to identify time-wasting practices, both large and small. One small issue that staff discovered was laptop power cords that continually fell on the floor, needing to be picked up. That fix was simple: securing them with oversized paper clips. Sharon Simpson, a registered nurse with the primary care practice, says staff also acquired new skills, such as learning how to do Excel spreadsheets and PowerPoint presentations. To undertake the journey towards greater efficiency, the practice teamed up with SKF business efficiency expert Matthew Metz in 2011. The goal was to improve the practice’s treatment of diabetes, a growing problem across the United States, due in part to high rates of obesity. Simpson says diabetes is increasingly affecting younger people. “The rising prevalence impacts health-care costs, especially because diabetes leads to all kinds of other problems – eye, cardiovascular and circulatory,” she says.
Recent data shows that Pennsylvania has the 12th-highest rate of diabetes amongst US states. Central Pennsylvania, where the practice is located, is home to several major snack food manufacturers. Metz, who is SKF’s business excellence manager and Six Sigma efficiency expert in Hanover, Pennsylvania, describes the region as the snack capital of the world. “We’re surrounded by temptation,” he says. To improve efficiency, Metz met weekly with the staff. He explains: “This was about data gathering, as opposed to the typical problem-solving approach based on ‘I think,’ ‘I remember,’ and ‘I’ve seen.’” The idea was not to be efficient for efficiency’s sake, but rather to improve the quality of medical care. “We wanted to work on waste reduction and time management so that we could spend more time with each patient,” Simpson says. The cooperation between SKF and the medical practice was forged by the Robert Wood Johnson Foundation as part of its larger initiative to improve health care in US communities, through an organization called Aligning Forces for Quality. Dr Adelle Kurtz, a physician specializing in family medicine, says when Metz first arrived at the York office, “we didn’t even know how many of our patients had diabetes.” It turned out that 800 of the practice’s 6,000 patients were diabetic. However, the office software wasn’t set up to identify them. “Before we had statistics about how we ran our office, we pretty much assumed we were doing fine,” Kurtz says. “But we learned there were areas where we could make improvements.” Margaret Lewis, the practice’s manager, says, “Our jobs have changed dramatically. We even gave accounting its own door.” All told, Metz and the staff identified 32 areas of inefficiency, eventually finding ways to address 27 of them. Most importantly, they found ways to improve the long-term care of patients with diabetes. Not all the changes occurred easily. “It was a little rocky at the start,” Simpson recalls. “All those spider charts – or were they spaghetti graphs?” Metz says his 24 years at SKF have taught him that people sometimes resist efficiency techniques, despite their effectiveness. “The practice did great work,” he says. “The statistics show that their efforts paid off. It was a learning experience for me, to see how long it took to make a difference.” Although Metz’s work with the practice is done now, the medical staff continues to meet biweekly to discuss ways it can improve, and it also shares its discoveries with other primary care groups in the region. In the long term, the practice hopes to win certification as a Patient-Centered Medical Home, a prestigious designation for medical practices that reach out to patients in a proactive way, rather than waiting for patients to get sick. “For patients with diabetes, the approach stresses self-management instead of just medications,” says Kurtz. The work has paid off, Simpson explains. In the region around York, improved patient management has already led to a drop in the number of emergency-room visits in the past two years. And that’s the kind of change that can keep US health-care costs from spiralling out of control.