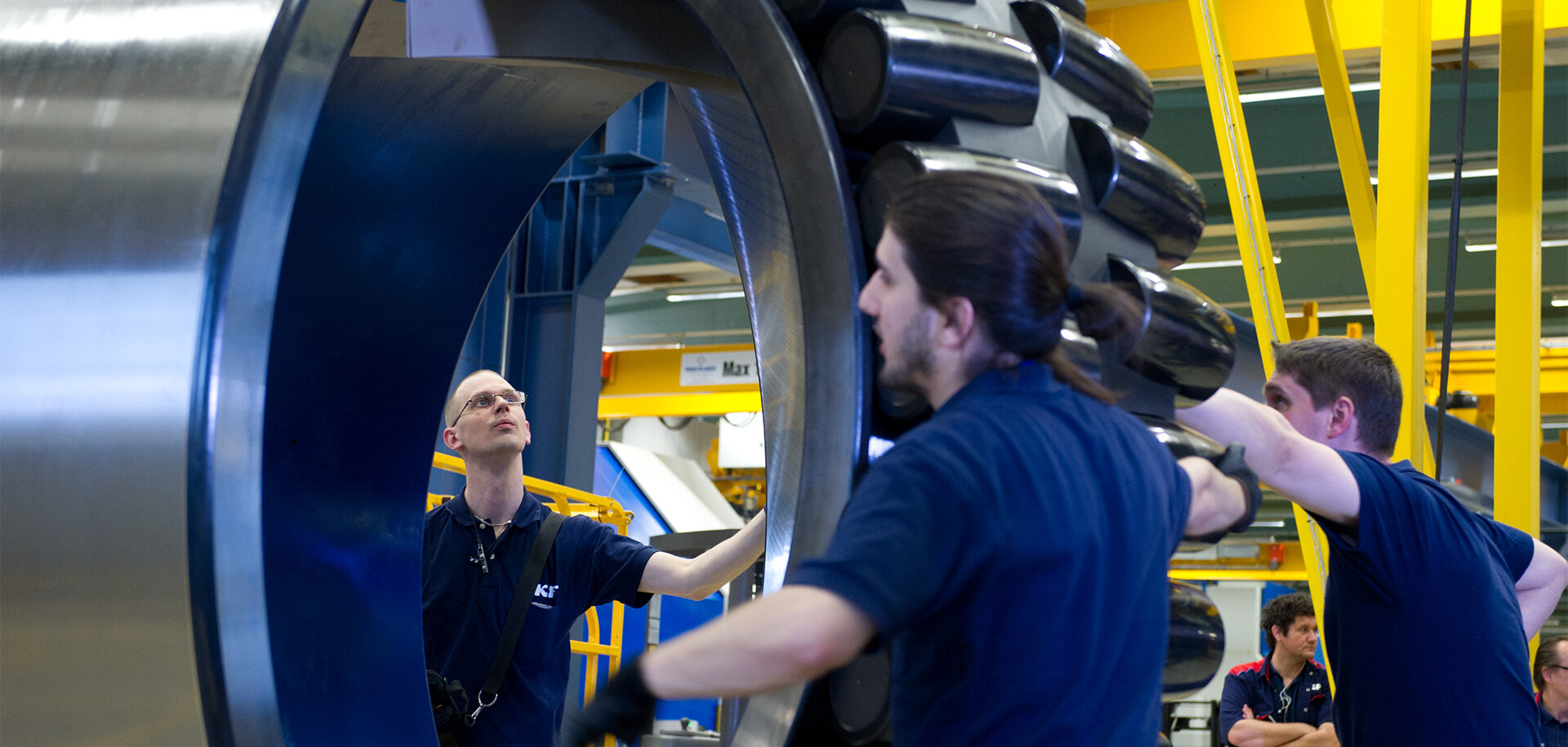
Rivestimenti per migliorare le prestazioni dei cuscinetti
I rivestimenti ottimizzano la durata di esercizio e le prestazioni dei cuscinetti volventi e radenti. Possono soddisfare un’ampia gamma di requisiti di prestazioni delle applicazioni e di condizioni di esercizio. Attualmente SKF offre più di 35 rivestimenti specifici differenti.
Oggi ci si attende che un cuscinetto volvente possa essere utilizzato e possa ruotare quasi all’infinito qualora siano soddisfatte tre condizioni operative: 1) le sollecitazioni applicate devono essere inferiori a un limite definito; 2) la lubrificazione deve essere adeguata; 3) non deve essere presente alcuna contaminazione. Naturalmente, in alcuni casi è possibile che un’applicazione sia tutt’altro che perfetta e che si possano verificare problemi inaspettati che potrebbero aumentare i costi di gestione e manutenzione.
Per migliorare la durata di esercizio e le prestazioni dei cuscinetti in presenza di condizioni non ideali sono state sviluppate diverse strategie. Una soluzione è ricorrere a rivestimenti in grado di potenziare svariate proprietà, tra cui:
- resistenza all’usura;
- aumento o riduzione dell’attrito;
- resistenza alla corrosione;
- miglioramento dello scorrimento e funzionamento in condizioni di emergenza;
- ottimizzazione della lubrificazione o riduzione della necessità di lubrificazione in esercizio;
- migliori proprietà di adesione del lubrificante;
- isolamento elettrico;
- barriera alla penetrazione dell’idrogeno;
- prevenzione della ruggine da contatto;
- miglioramento dell’aspetto estetico.
Il rivestimento di un substrato in acciaio di un cuscinetto standard con materiali che svolgono le funzioni desiderate può migliorare notevolmente le prestazioni dell’intero cuscinetto. I cuscinetti con rivestimento si possono utilizzare anche per colmare il divario tra i cuscinetti standard in acciaio e i cuscinetti ibridi in ceramica. Per alcune applicazioni una buona soluzione sarebbe l’uso di corpi volventi in ceramica, ma è piuttosto costosa e talvolta non disponibile in commercio. In questi casi è possibile portare il funzionamento dei cuscinetti standard al livello desiderato applicando dei rivestimenti.
Alcuni rivestimenti vengono depositati in strati molto sottili e questo è un grande vantaggio. L’impiego di rivestimenti con uno spessore dell’ordine di pochi micron consente infatti di utilizzare cuscinetti standard prelevati dalle linee produttive senza dover effettuare costosi cambi sui macchinari.
Panoramica delle tecniche di rivestimento
SKF utilizza diverse tecniche di rivestimento, come illustrato in figura 1, che possono essere suddivise in tre categorie principali:
- Processi allo stato gassoso, in cui il materiale di rivestimento passa attraverso una fase gassosa o di vapore prima di essere depositato sulla superficie. Questi includono processi di deposizione da fase vapore come PVD (Physical Vapour Deposition) e PACVD (Plasma-Assisted Chemical Vapour Deposition).
- Processi in soluzione, in cui il materiale di rivestimento è presente in fase liquida prima di essere depositato come solido sulla superficie. I metodi si possono suddividere nelle categorie di deposizione chimica (ad esempio, deposizione senza elettrolisi, conversione chimica, reazioni chimiche omogenee, immersione e spruzzo di liquidi) e deposizioni elettrochimiche, come la deposizione galvanica di un rivestimento metallico su un elettrodo mediante un processo di elettrolisi.
- Processi allo stato fuso, in cui il materiale di rivestimento viene fuso o parzialmente fuso (ammorbidito) prima di essere depositato come solido sulla superficie mediante l’impiego di una fonte di energia a temperatura elevata. I metodi si suddividono in deposizione a spruzzo (che copre un’ampia gamma di tecniche in cui il materiale viene riscaldato rapidamente in un mezzo gassoso a temperatura elevata e contemporaneamente spruzzato ad alta velocità su una superficie per produrre un rivestimento) e tecnica di rivestimento laser.
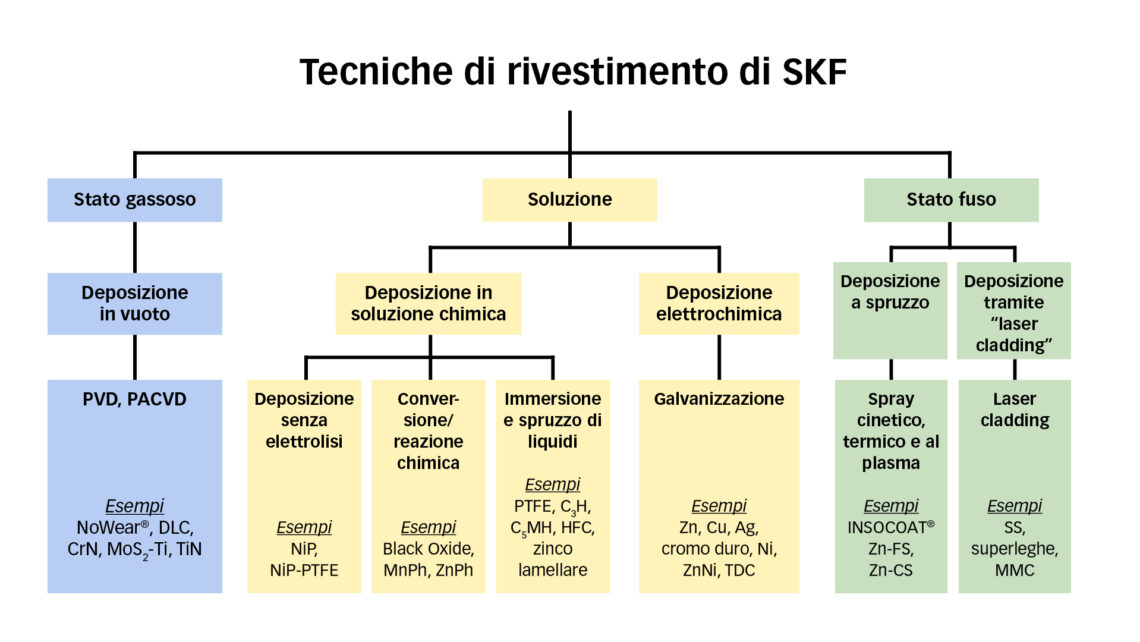
Mondo dei rivestimenti di SKF
SKF ha un assortimento di oltre 35 diversi rivestimenti all’avanguardia utilizzabili in molteplici applicazioni o in diverse parti dei cuscinetti. Tutti i rivestimenti sono stati ottimizzati per le esigenze particolari dei cuscinetti e si basano su specifiche precise e su un rigoroso controllo di qualità. Sono prodotti in impianti di rivestimento di primo livello, che spesso vanno ben oltre i normali standard dei rivestimenti e delle attrezzature e offrono il massimo in termini di qualità, affidabilità e ripetibilità.
Alcuni rivestimenti vengono depositati in strati molto sottili e questo è un grande vantaggio.
In questo articolo saranno approfonditi alcuni dei rivestimenti di SKF utilizzati più spesso. L’elenco completo dei rivestimenti di SKF, insieme alle relative proprietà fisiche e tribologiche e a tutte le applicazioni, è stato recentemente pubblicato nel catalogo online SKF Coatings.
Cuscinetti volventi
Per quanto riguarda i cuscinetti volventi, in figura 2 sono riportati 12 rivestimenti principali che svolgono cinque funzioni indispensabili per le applicazioni con tali cuscinetti, tra cui antiusura da strisciamento sulle gabbie, isolamento elettrico, ruggine da contatto, anticorrosione e antiusura sulle piste.
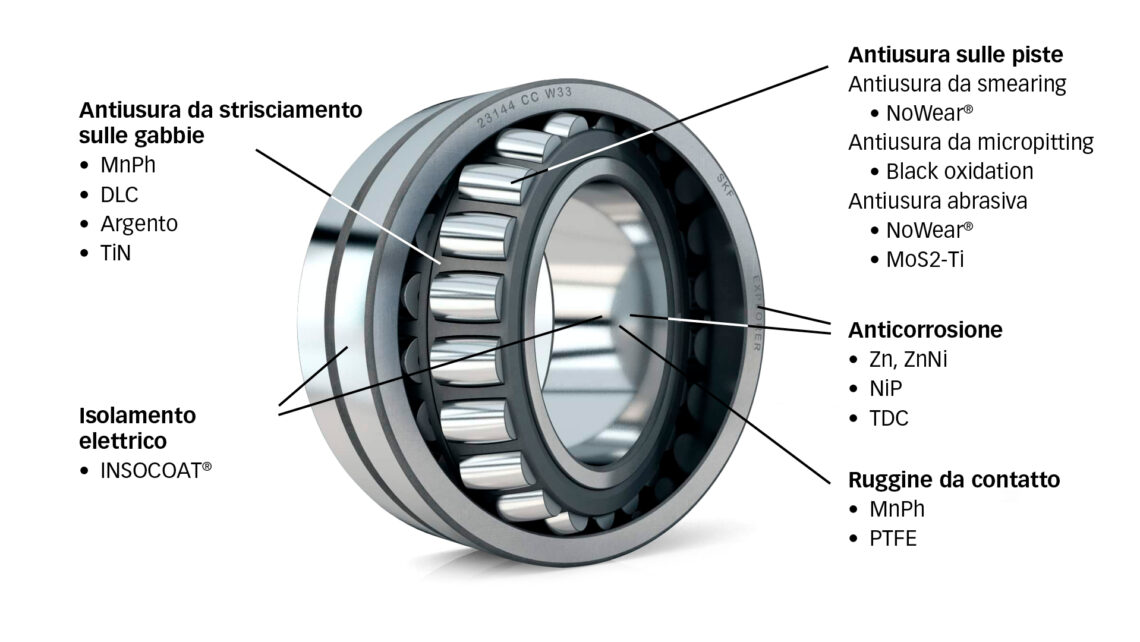
a. Antiusura sulle piste
Black oxidation: si tratta di un trattamento superficiale realizzato sulla superficie dell’acciaio del cuscinetto mediante una reazione chimica. Il rivestimento può essere applicato su tutti i componenti dei cuscinetti. Le parti vengono immerse in diverse soluzioni saline acquose alcaline con temperature comprese nell’intervallo 140-150 °C. La reazione tra il ferro della lega di acciaio e i reagenti produce uno strato di black oxidation di circa 1 μm di spessore, costituito da una miscela ben definita di ossido ferroso (FeO), ossido ferrico (Fe2O3) e ossido ferroso-ferrico (Fe3O4). Il rivestimento offre numerosi vantaggi, come la riduzione dell’usura da strisciamento e dell’usura adesiva. Migliora anche il rodaggio grazie alla superficie molto liscia e all’attrito finale costantemente inferiore rispetto ai cuscinetti privi di rivestimento. Un altro vantaggio è rappresentato dall’aumento dell’adesione dell’olio alla superficie, che assicura una leggera protezione dalla corrosione. La black oxidation protegge l’acciaio sottostante perché agisce anche come barriera contro la penetrazione dell’idrogeno. Inoltre, aumenta la resistenza a micropitting, smearing, erosione, corrosione da movimento relativo, formazione di cricche superficiali e fatica prematura. Infine, protegge la superficie dagli additivi EP talvolta dannosi, spesso utilizzati nei lubrificanti per moltiplicatori di giri utilizzati nel settore delle turbine eoliche.
NoWear®: SKF è stata la prima azienda di cuscinetti al mondo a utilizzare rivestimenti a base di carbonio sui cuscinetti. Su tutti i componenti della superficie del cuscinetto è possibile applicare un rivestimento, ma i risultati migliori si ottengono rivestendo solo i rulli. I componenti vengono introdotti in una camera a vuoto in cui viene utilizzato il metodo PACVD: reazioni chimiche e fisiche in presenza di plasma producono una miscela di vapori di carbonio e metallo che si condensano sul pezzo in lavorazione a temperature inferiori a 180 °C. Il rivestimento amorfo grigio scuro risultante, cha ha uno spessore di circa 3 μm, una durezza moderata e un attrito molto basso anche allo stato secco, è ottimizzato per l’impiego sulle piste dei cuscinetti in presenza di pressioni di contatto elevate. Il rivestimento NoWear®, brevettato nel 1999, riduce l’adesione, lo smearing, la fatica superficiale e il micropitting e garantisce un’usura ridotta in condizioni di scarsa lubrificazione. Inoltre, il rivestimento multistrato ingegnerizzato contiene uno strato inferiore speciale per potenziare l’adesione e uno strato superiore a base di grafite per migliorare il rodaggio.
MoS2+Ti: si tratta di uno strato amorfo di disolfuro di molibdeno (MoS2) additivato con titanio (Ti) di circa 1-3 μm di spessore, di durezza simile a quella del rivestimento NoWear®, ma appositamente progettato per avere un attrito molto basso e un’elevata resistenza all’usura in ambienti asciutti, sotto vuoto e in camera bianca. I componenti vengono introdotti in una camera a vuoto dove viene utilizzato il metodo PVD: reazioni fisiche in presenza di plasma producono un vapore che si condensa sul pezzo in lavorazione a temperature inferiori a 180 °C.
b. Anticorrosione
Zn e ZnNi: lo zinco e la lega zinco-nichel sono strati dello spessore di 1-15 μm, depositati con metodi elettrolitici e successivamente passivati per una maggiore protezione. In genere si realizzano sulle superfici esterne dei cuscinetti. Per quanto riguarda l’anticorrosione, sebbene tradizionalmente si utilizzasse lo zinco, la lega con il nichel ha permesso di superare alcuni degli svantaggi del rivestimento di zinco puro, come la sua durezza ridotta. Oltre alle sue proprietà anticorrosione, lo zinco offre un attrito elevato utilizzabile per una funzione antislittamento o di resistenza al fretting nelle superfici esterne dei diametri esterni dei cuscinetti, dei diametri interni o dei fori dei supporti dei cuscinetti.
NiP: la lega di nichel-fosforo color argento con uno spessore compreso tra 10 e 50 μm viene depositata con un metodo autocatalitico senza elettrolisi. Esistono tre varianti con diverse concentrazioni di fosforo, comprese tra il 6 e il 14%; l’aumento del fosforo migliora le proprietà anticorrosione, ma pregiudica la durezza e la resistenza all’usura. Tipicamente realizzato sulle superfici esterne dei cuscinetti, in cui è richiesta una combinazione di proprietà anticorrosione e antiusura, questo rivestimento può essere utilizzato anche in piste con spessori inferiori a 3 μm.
TDC (sottile strato di cromo ad alta densità): si tratta di uno strato di cromo policristallino di colore argento di spessore compreso tra 2 e 5 μm. Il rivestimento viene realizzato per elettrolisi con un elettrolita a base di acido cromico. Il processo viene ulteriormente catalizzato, ad esempio, con bicromato di potassio per formare un sottile strato di cromo con struttura nodulare. I sottili strati di cromo ad alta densità si possono applicare sulle piste e sulle superfici esterne dei cuscinetti. Oltre a un’ottima resistenza alla corrosione, il rivestimento presenta un’elevata durezza, un basso attrito e un’alta resistenza all’usura.
c. Ruggine da contatto
PTFE: si tratta di un rivestimento polimerico dello spessore di 10-20 μm. La polvere di politetrafluoroetilene (PTFE) viene spruzzata sulla superficie mediante deposizione elettrostatica o atomizzazione ad aria e lo strato si forma attraverso un processo di sinterizzazione termica. Il rivestimento ha eccellenti proprietà di strisciamento, un attrito molto basso e nessuna proprietà di stick-slip. Conferisce ai cuscinetti proprietà di resistenza al fretting eccezionali e permanenti nei diametri interni o esterni degli anelli dei cuscinetti.
d. Isolamento elettrico
INSOCOAT®: si tratta di uno strato isolante di ossido di alluminio di circa 100-300 μm di spessore, applicato con un processo di spray al plasma atmosferico. Le particelle di ossido di alluminio (Al2O3) fuso vengono spruzzate sul substrato di acciaio e la struttura porosa viene successivamente sigillata. Un’ulteriore fase di rettifica di finitura contribuisce a garantire le dimensioni corrette dei cuscinetti. Il rivestimento viene applicato sulle superfici esterne dell’anello esterno del cuscinetto o sulla superficie interna del foro dell’anello interno. I principali vantaggi di INSOCOAT® sono legati all’isolamento elettrico; questo rivestimento infatti impedisce il passaggio di corrente elettrica attraverso il cuscinetto, che causa l’erosione delle superfici di rotolamento.
e. Antiusura da strisciamento sulle gabbie
Ag: strati di argento (Ag) con spessori compresi tra 2 e 4 μm sono depositati con metodi galvanici, di solito con uno strato sottostante in rame per aumentarne l’adesione. È un rivestimento metallico poco resistente con proprietà di lubrificazione a secco, utilizzato a temperature elevate e in ambienti sotto vuoto. Ha un’eccellente conducibilità elettrica e un’ottima protezione dalla corrosione contro gli agenti chimici (alcalini e acidi moderati). Si utilizza principalmente per la placcatura di gabbie in acciaio e, in rari casi, di anelli e rulli per alcune applicazioni gravose, come la lubrificazione a secco in applicazioni sotto vuoto, nel settore alimentare e in quello aerospaziale.
TiN: i rivestimenti al nitruro di titanio (TiN) sono strati di colore dorato con spessori compresi tra 1 e 5 μm. I componenti vengono introdotti in una camera a vuoto in cui viene utilizzato il metodo PVD: reazioni fisiche in presenza di plasma a base di azoto producono un vapore che viene spruzzato da una superficie di destinazione in titanio e si condensa sul pezzo in lavorazione a temperature inferiori a 180 °C. Sono utilizzati come rivestimenti resistenti all’usura per gabbie in presenza di lubrificanti e per bussole con rivestimento nel settore alimentare.
Cuscinetti radenti
Per quanto riguarda i cuscinetti radenti, in figura 3 sono riportati otto rivestimenti principali che svolgono tre funzioni indispensabili per le applicazioni con tali cuscinetti: rivestimenti anticorrosione e antiusura per cuscinetti con o senza lubrificazione a grasso.
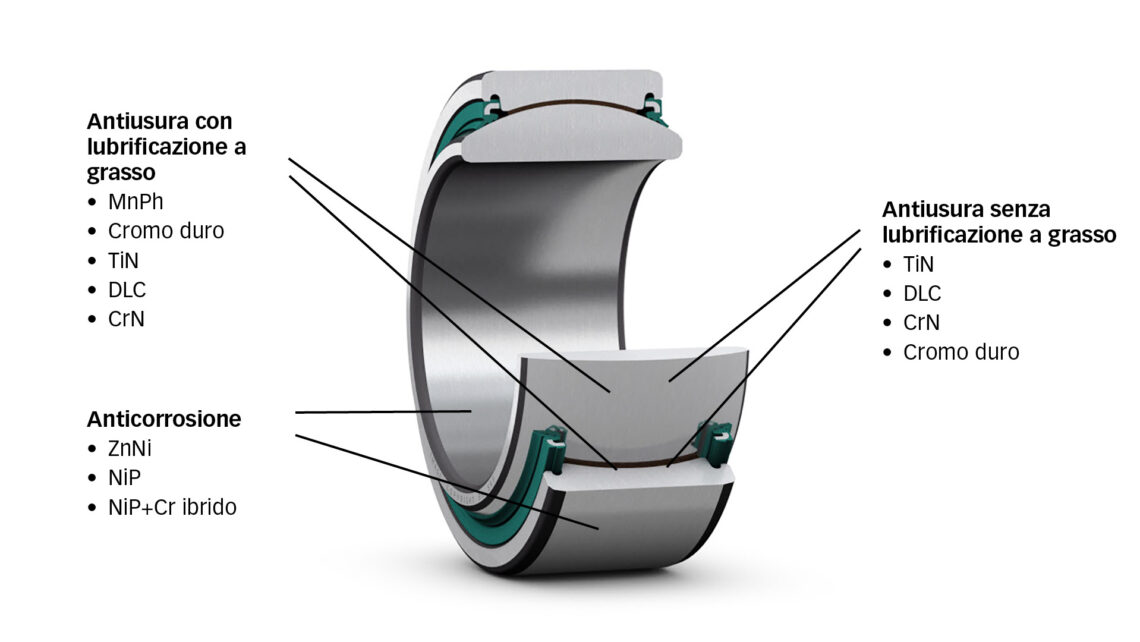
a. Antiusura senza lubrificazione a grasso
Cromo duro: si tratta di uno strato di cromo duro di colore argento, di spessore compreso tra 3 e 15 μm, depositato mediante un processo di galvanizzazione con un elettrolita a base di acido cromico. Il processo si conclude con la pulizia, la rimozione del cromo esavalente [Cr(VI)] e la conservazione dell’olio. Il rivestimento garantisce un contatto di strisciamento ottimale tra i componenti del cuscinetto radente, con un’elevata durezza e un’alta resistenza all’usura. Lo strato di cromo risultante presenta microcricche, il che significa proprietà anticorrosione limitate in caso di spessori ridotti.
CrN: il nitruro di cromo (CrN) è uno strato di colore grigio-argento depositato mediante PVD con spessori compresi tra 1 e 6 μm. I componenti vengono posti in una camera a vuoto, in cui superfici di destinazione solide in cromo puro vengono bombardate con un plasma a base di ioni di argo e azoto che vaporizzano il materiale in cromo (processo di vaporizzazione). Gli atomi di cromo si combinano con l’azoto e si condensano sui pezzi in lavorazione mantenuti a una temperatura inferiore a 180 °C. Con questo processo si ottiene un rivestimento duro che offre ottime prestazioni nelle applicazioni con usura da strisciamento e in alcuni ambienti corrosivi. Il rivestimento può essere utilizzato anche in applicazioni con cuscinetti volventi, combinando anelli con rivestimento in nitruro di cromo e rulli con rivestimento NoWear®. Il rivestimento viene utilizzato anche come strato sottostante di altri rivestimenti per aumentare la resistenza alla pressione di contatto.
DLC (carbonio diamantato): si tratta del nome generico di un gruppo di rivestimenti a base di carbonio con composizioni contenenti una miscela di microstrutture di grafite e diamante. Possono contenere o non contenere idrogeno e lo spessore in genere è compreso tra 2 e 4 μm. I componenti da rivestire vengono posti in una camera a vuoto, in cui vengono applicati diversi strati sulle superfici dei componenti del cuscinetto utilizzando il processo PVD o PACVD a seconda dell’applicazione. La loro composizione influisce sulle proprietà dei rivestimenti. I rivestimenti DLC sono progettati per condizioni con usura elevata e scarsa lubrificazione. Presentano un’elevata resistenza all’usura adesiva e da strisciamento, una maggiore capacità di carico, un’eccellente protezione dall’abrasione e un basso attrito; inoltre proteggono la superficie in condizioni di scarsa lubrificazione. I rivestimenti DLC sono ideali per cuscinetti radenti, azionamenti lineari dei cuscinetti, alberi dei cuscinetti, boccole, perni delle rotelle e componenti di strisciamento nei cuscinetti radenti (come gabbie e tenute). Il rivestimento a base di metallo e carbonio ingegnerizzato NoWear® fa parte della linea di rivestimenti a base di carbonio; tuttavia, presenta alcune differenze. I valori di durezza dei rivestimenti DLC per applicazioni di strisciamento sono compresi nell’intervallo 18-30 GPa (1.800-3.000 HV), mentre i rivestimenti NoWear® (impiegati nelle applicazioni di rotolamento) presentano valori di durezza di circa 12 GPa (~ 1.200 HV).
b. Antiusura con lubrificazione a grasso
MnPh: il fosfato di manganese (MnPh) è uno strato grigio-nero con uno spessore compreso tra 2 e 15 μm. Il rivestimento viene applicato mediante una reazione chimica e in genere su tutte le superfici del pezzo in lavorazione. I componenti vengono immersi in un fluido a base di fosfato di manganese; l’acciaio dei pezzi in lavorazione reagisce con i cationi di manganese e con gli anioni di fosfato contenuti nel fluido. Il rivestimento ha proprietà antiusura e di resistenza al fretting e migliora in modo significativo la resistenza allo smearing e al micropitting. Garantisce anche protezione in condizioni di scarsa lubrificazione con valori bassi di kappa e genera una migliore adesione dell’olio. Inoltre il fosfato di manganese presenta un’ottima protezione dalla corrosione (in condizioni di lubrificazione) e possiede proprietà di isolamento elettrico.
c. Anticorrosione
NiP+Cr ibrido: si tratta di un doppio strato duro di colore argento di rivestimenti di nichel-fosforo e cromo con uno spessore compreso tra 10 e 30 μm. Il processo di rivestimento completo è costituito da due fasi distinte. Innanzitutto sulla superficie viene applicato uno strato di nichel-fosforo senza elettrolisi per migliorare la protezione dalla corrosione e conferire resistenza chimica; successivamente viene aggiunto uno strato di cromo duro per deposizione elettrolitica per ottenere una maggiore resistenza meccanica.
I rivestimenti, la strada verso la sostenibilità
La sostenibilità nel settore dei cuscinetti comprende aspetti quali la conservazione dell’energia e delle risorse, la riduzione al minimo dei rifiuti, il miglioramento dell’efficienza dei processi e l’impiego di materiali rinnovabili. In qualità di leader tecnologico globale SKF considera la trasformazione tecnologica di oggi una responsabilità e una grande opportunità. Il riutilizzo di materiali e componenti industriali, come olio e cuscinetti, è un buon punto di partenza. L’offerta – dai cuscinetti e dalle tenute fino ai componenti e ai sistemi industriali principali – può contribuire, ad esempio, a sviluppare soluzioni leggere e a basso attrito per il settore automobilistico che possano ridurre le emissioni di CO2. Un altro approccio sostenibile prevede di sfruttare le tecniche di rivestimento, che in alcune applicazioni riducono l’attrito, e di conseguenza il consumo di energia, e prolungano la durata di esercizio dei cuscinetti, riducendo quindi il consumo di nuove materie prime.
Osservazioni conclusive
L’impiego dei rivestimenti nelle applicazioni di cuscinetti sta incontrando un favore sempre maggiore. La scelta di materiali e architetture di rivestimento consente di personalizzare proprietà fisiche, meccaniche e tribologiche uniche per soddisfare le crescenti esigenze tecnologiche. In particolare, i rivestimenti di SKF sono stati studiati con estrema attenzione per assicurare proprietà ottimali e in alcuni casi i processi sono stati adattati alle diverse applicazioni andando oltre le norme DIN e ISO.
In questo articolo sono state illustrate brevemente alcune delle diverse tipologie di rivestimenti di SKF per fare chiarezza sulla terminologia, sugli aspetti tecnici e sulla progettazione dei rivestimenti. Per maggiori informazioni fare riferimento al catalogo SKF Coatings.