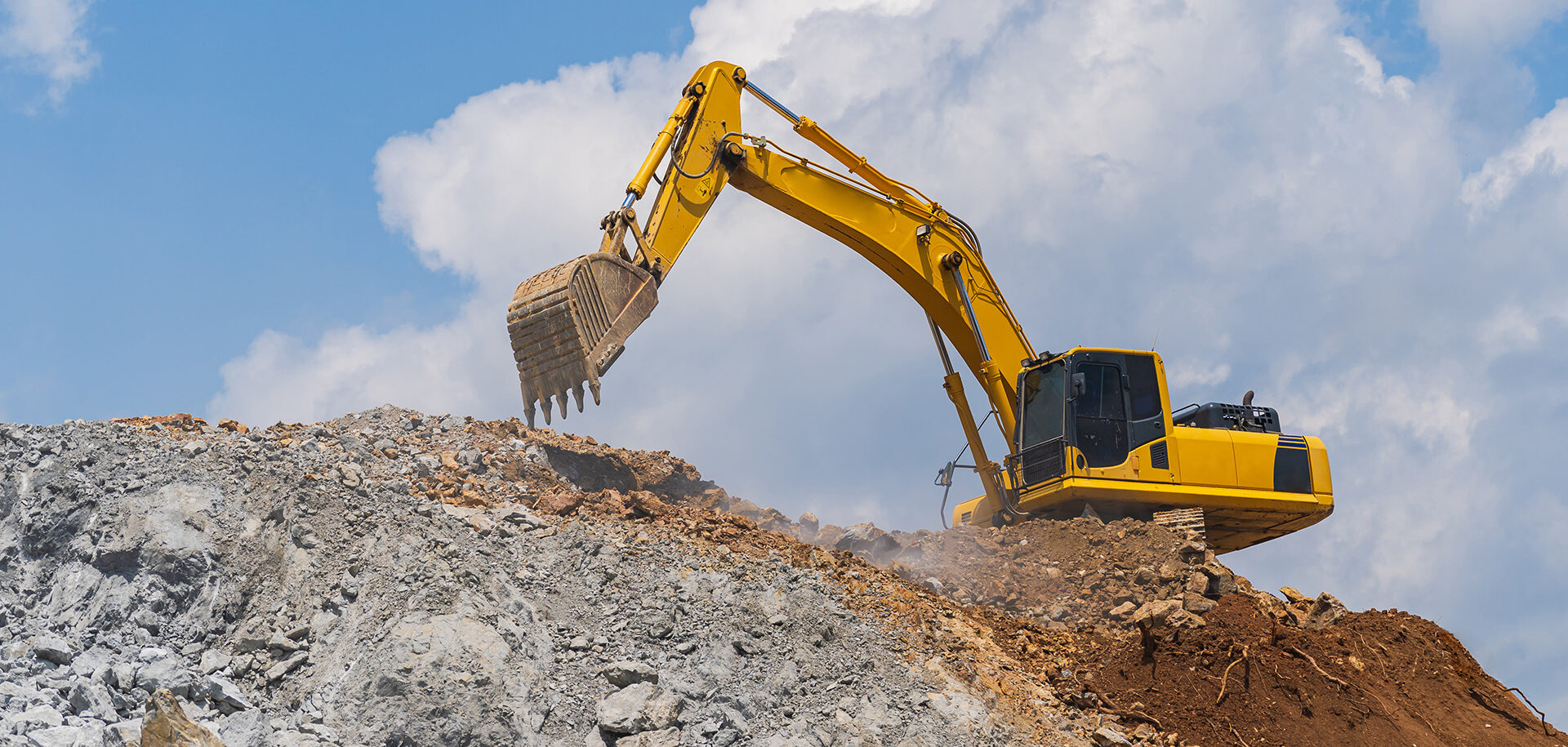
摩擦优化的缓冲密封延长液压缸的使用寿命
在液压系统中,通过对液体加压产生液体动力,随后液体动力经控制并转化为活塞的往复运动,其效率由输出能量与输入能量之间的比值来确定。密封对液压系统的效率影响很大,因为它们是液压缸中受压区两侧的屏障,并且与运动部件(活塞杆和活塞)直接接触。
密封产生的摩擦力会阻碍移动,降低能量输出。摩擦增大不仅会影响能量输出,也会造成工作温度升高,导致整个液压密封系统的使用寿命缩短。温升还会影响液压油的特性,尤其是油的粘度,从而导致润滑性能下降和能量输出减少。除此之外,被称为爬行现象的摩擦力波动也会影响定位精度并产生噪音。
“可持续性”的重要性日益凸显,已经渗透到世界每个角落。可持续的液压系统必须确保无泄漏,而且停机维护间隔时间必须尽可能长。从密封的角度来看,要达到此目标,需要选择尽可能好的密封系统(包括活塞杆密封、活塞密封以及导向环和静密封),以获得最大效率。因此,不仅必须了解密封类型,还必须熟知不同密封类型之间的相互作用,才能实现高效密封系统的目标。
本文重点探讨液压设备(例如挖掘机)中使用的活塞杆密封系统。尤其是通过内部试验台研究和有限元分析对缓冲密封与主活塞杆密封之间的相互作用进行了深入研究。在这些研究的基础上,SKF新开发了两种摩擦优化的缓冲密封。
液压活塞杆密封系统及其主要密封功能
液压缸中的活塞杆密封系统通常包括一个缓冲密封、一个主活塞杆密封和一个防尘圈(图1)。
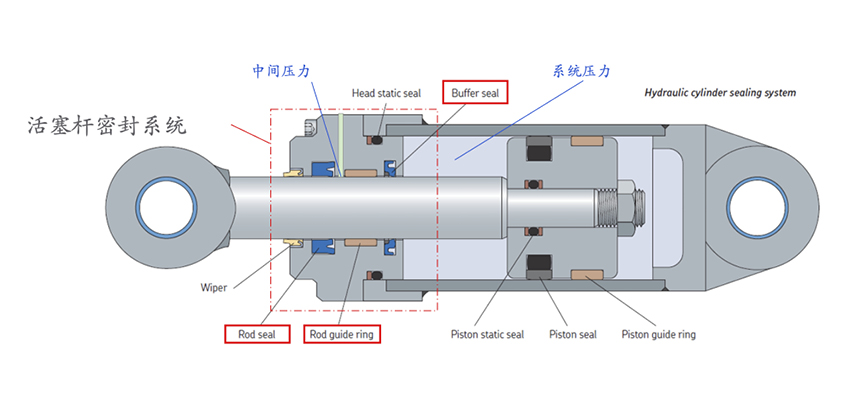
缓冲密封的主要作用如下:
- 吸收可能损坏主活塞杆密封的系统峰值压力 (P峰值)
- 允许液压油通过密封唇口,从而为主活塞杆密封和防尘圈提供润滑(见图 2)
- 当系统压力低于中间压力时,排放缓冲密封件和主活塞杆密封件之间的中间压力(见图 1),以防止出现困压现象
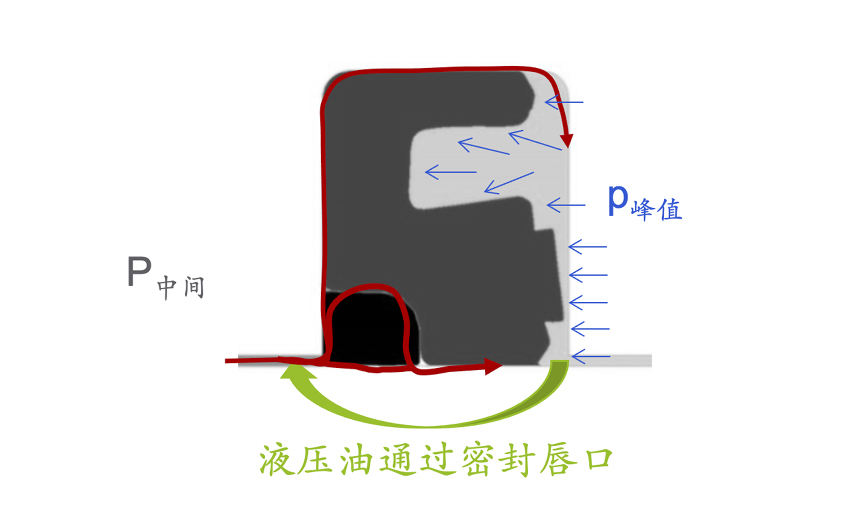
主活塞杆密封与缓冲密封组合使用具备以下功能:
- 通过减少油膜厚度来防止泄漏,并允许油液反向泵回系统
- 保持适当的油膜厚度,既要尽可能减少泄漏,又要尽量降低摩擦力
- 承受可能出现的中间压力
防尘圈具备以下主要功能:
- 阻隔来自周边的各种污染物
- 能将液压油泵送回系统,以防止泄漏
- 释放活塞杆密封和防尘圈之间可能出现的中间压力
缓冲密封类型
为了实现上述缓冲密封的功能并提高活塞杆密封系统的效率,缓冲密封的设计需要确保主活塞杆密封和防尘圈具有一定的油膜厚度。
通常,市场上有两种不同类型的缓冲密封,其工作原理不尽相同。第一种类型称为“高密封性缓冲密封”。它侧重于尽可能地减小油膜的厚度,从而防止主活塞杆密封受压。一方面,这类密封可以防止由压力引起的主活塞杆密封的挤出以及磨损,但另一方面它会导致活塞杆密封的润滑不足,从而摩擦增大,系统温度升高,并可能诱发爬行现象。
第二种类型称为“摩擦优化的缓冲密封”。这类密封允许一定的油膜通过密封唇,从而确保主活塞杆密封有足够的润滑。一方面,这类密封可能会导致缓冲密封后面出现中间压力,该中间压力必须由主活塞杆密封来承受,但另一方面它减少了整个活塞杆密封系统的摩擦,从而可延长使用寿命并提高效率。
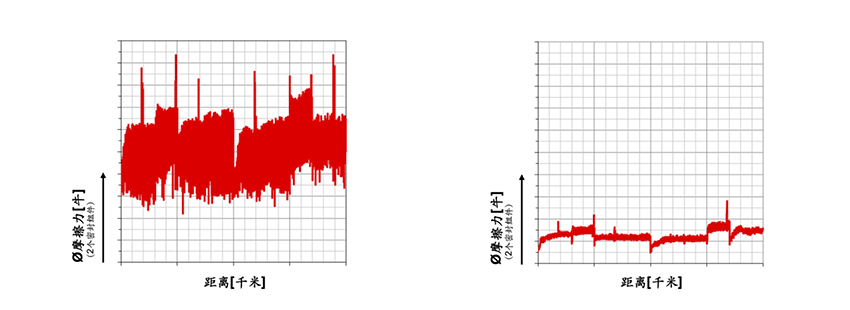
SKF在内部试验台研究中比较了这两种缓冲密封,并了解到这两种类型在市场上都有一席之地,而SKF专注于开发摩擦优化的缓冲密封,以尽可能地提高效率。
1.1 SKF开发的摩擦优化的缓冲密封
SKF开发了两种全新的摩擦优化的缓冲密封。一种是针对重载应用场合进行了优化设计的HDB,它使用热塑性挡圈来防止挤出。另一种是针对中等载荷应用场合而设计的RDB,它使用高性能硬质聚氨酯材料制造。这两种缓冲密封的验证试验均已成功完成,但不同尺寸的现场验证试验仍在进行中(有的可能会持续一年之久)。
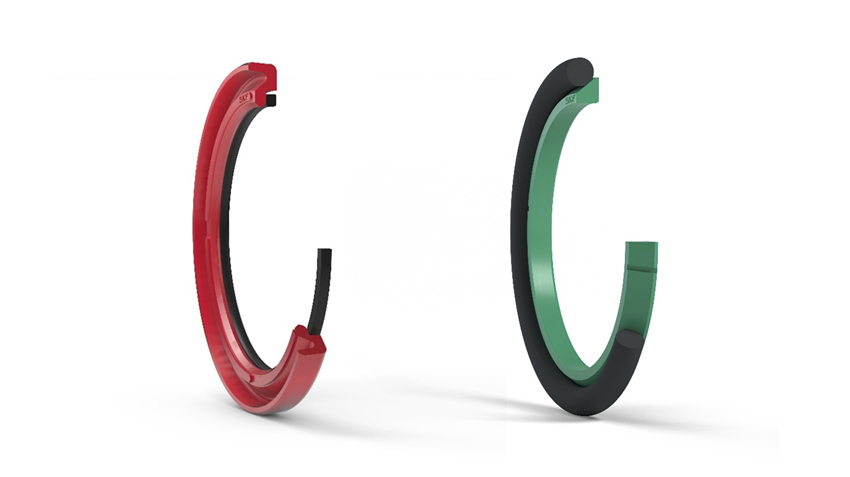
1.2 影响活塞杆密封组件效率的因素
正如引言中所述,若干因素会影响液压系统中活塞杆密封组件的效率。为了提高活塞杆密封系统的效率,必须将密封产生的摩擦力保持在最低水平。但密封的摩擦力受什么因素影响呢?
为了解答这个问题,我们需要仔细研究密封和运动部件之间的接触区域。影响因素完全可以用雷诺方程解释。根据该方程,两个表面之间薄油膜的流动受速度、接触压力分布梯度和油液粘度的影响。油膜越薄,摩擦力增加的可能性就越大。参见 /3/和/4/中的详细信息。
以普通U形活塞杆密封为研究对象,我们分析了活塞杆内外行程中,不同的速度对油膜厚度的影响。图5表明,随着外行程与内行程速度比的升高,泄漏相应的升高,油膜厚度升高。因此,如果外行程速度远高于内行程速度,则发生泄漏可能性更大。反之,如果内行程速度远高于外行程速度,则润滑不足的可能性增大,因此内行程速度高时摩擦力会增加。
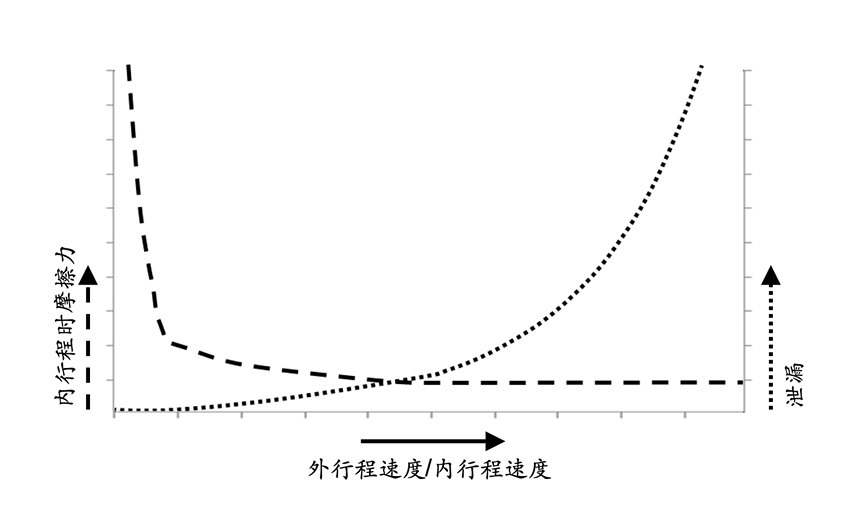
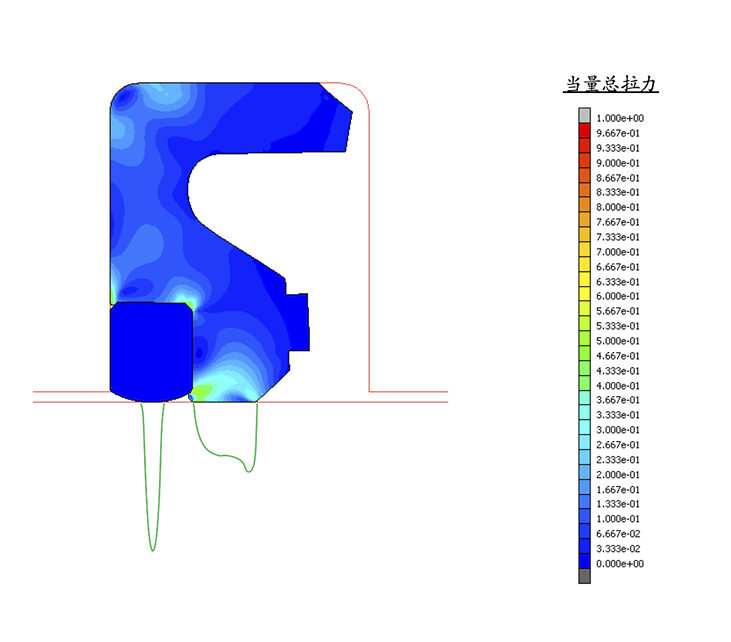
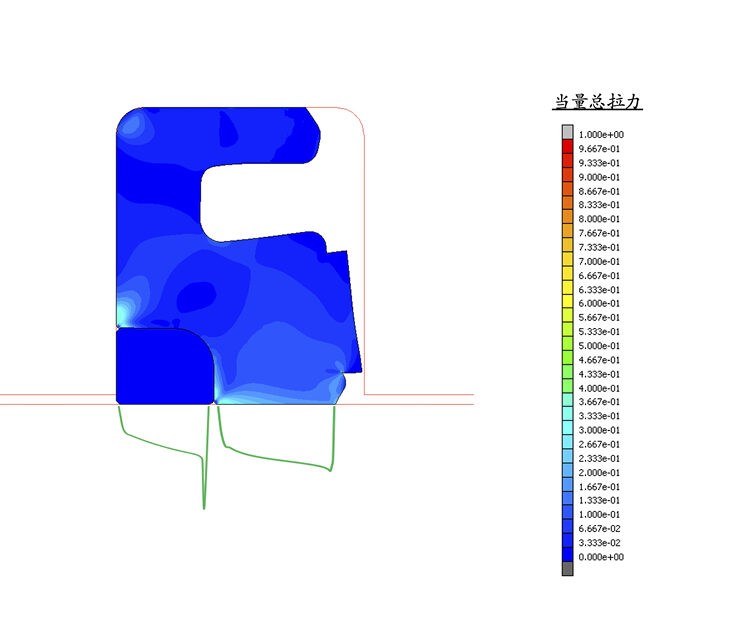
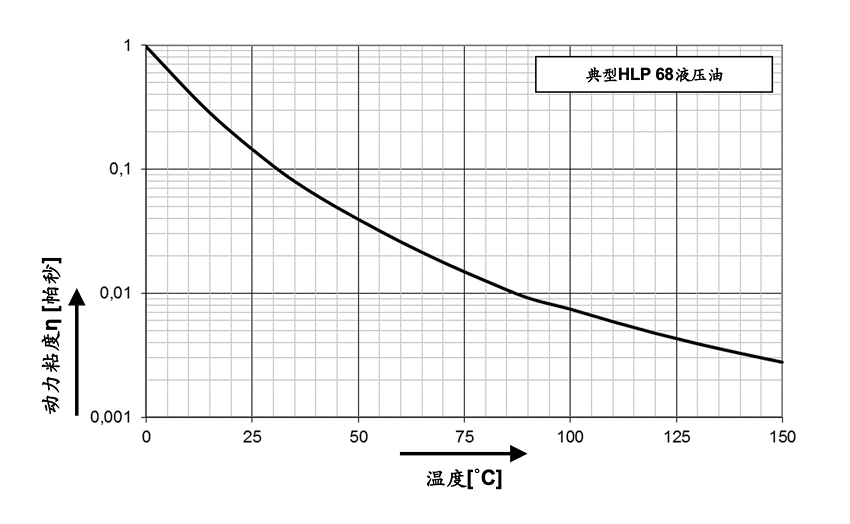
试验台研究
1.3 试验台配置
图9显示的是用于研究的试验台原理图和试验参数表。试验台由一个加压试验装置组成,包括缓冲密封和主活塞杆密封,以及静密封和导向环。该试验台还配备了一个可移动的活塞杆(电动)、一个液压增压单元和一个带有拉力及压力传感器的摩擦力检测系统。
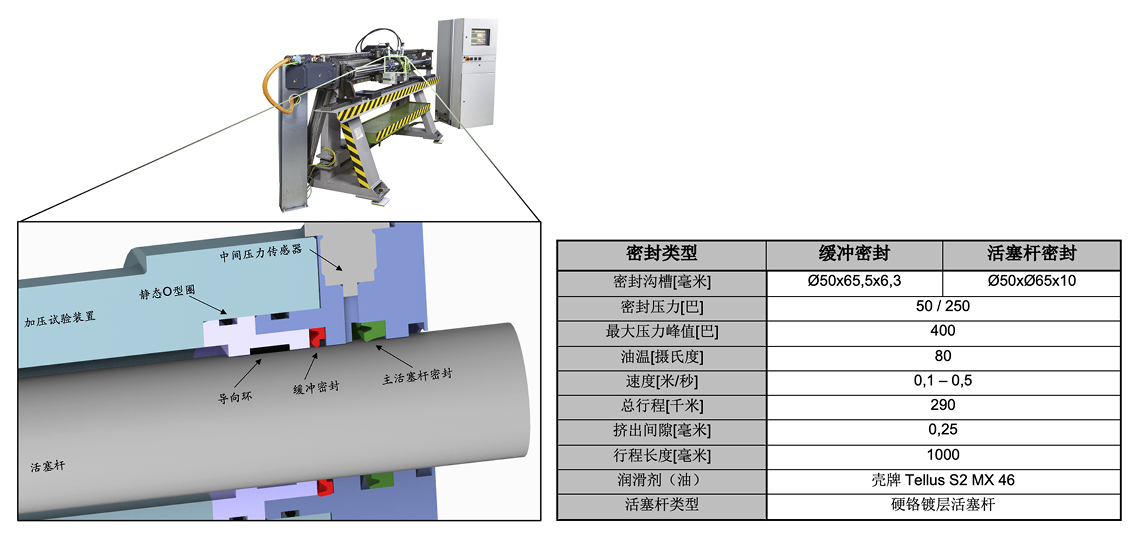
图10显示的是耐久试验旨在评估密封在使用寿命内最大截断压力和释放中间压力的能力。明确试验周期旨在验证所有缓冲密封功能,同时还要尽可能接近实际应用。试验程序包括以下试验阶段:
- 磨合阶段,为每个组件设置恒定启动条件,以确保能够进行正确的对比
- 前期性能试验阶段,以评估吸收压力峰值或形成中间压力的时间等特性
- 长时间试验阶段,评估耐磨性或抗挤出性等特性
- 后期性能试验阶段,评估密封的老化特性
结果和讨论
1.5 SKF新推出的HDB——用于重载应用场合(例如挖掘机)的缓冲密封
在耐久试验程序中,对与S1S主活塞杆密封组合的新型HDB缓冲密封进行了评估,并与用作试验基准的活塞杆密封组件进行了比较,基准组件由一个高密封性缓冲密封和一个带一体式挡圈的橡胶U形主活塞杆密封组成。
图11显示了前期及后期性能试验周期中的摩擦力以及直观分析。在比较摩擦力时,可以清楚地看出“摩擦优化的”缓冲密封 (SKF HDB) 和“高密封性”缓冲密封(基准)之间的区别。此外,与前期性能试验相比,基准组件在后期性能试验的摩擦显著上升。由于摩擦增加会导致运行温度升高,这意味着基准组件在长时间试验周期中受到了损害。SKF组件则展示出非常稳定和较低的摩擦力,这表明此密封系统可长期工作。
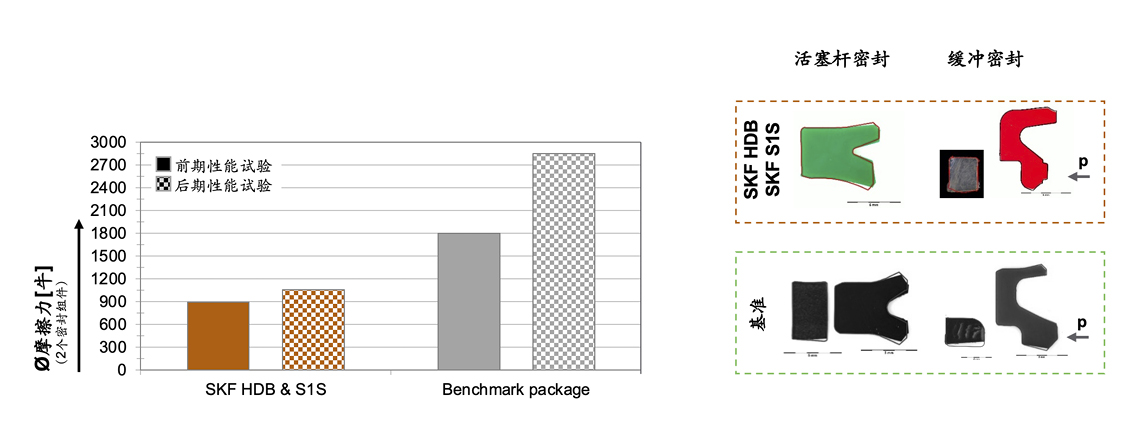
HDB和S1S几乎未出现挤出或磨损形式的损坏。SKF HDB的挡圈处只有轻微的尾部挤出,密封元件几乎没有可见的损坏,与SKF HDB组合使用时,活塞杆密封唇口预紧力受到的影响较小,这是因为较好的润滑可降低工作温度。
基准组件的摩擦增加导致整个系统温度升高,从而造成热塑性挡圈的磨损增加。除此之外,对主活塞杆密封的直观分析表明,由于温度升高和润滑不足,密封唇口预紧力损失增大。
在基准组件中,缓冲密封和活塞杆密封之间没有中间压力。而SKF组件显示出相对较低的中间压力,这得益于HDB的设计理念。无论如何,图11中的S1S截面形状表明中间压力并没有损坏主活塞杆密封。随着密封老化,HDB挡圈的变形则会产生更好的密封性,使得形成中间压力和润滑水平下降的可能性降低。在整个耐久试验后,两个组件均未出现泄漏。
研究表明,SKF组件由于摩擦力低,所需的功率输入更少,因而效率更高,其密封和油液的使用寿命更长,维护间隔时间更长。
1.6 SKF新推出的RDB——用于中等载荷场合(例如叉车)的缓冲密封
图12显示了SKF RDB和常用带橡胶弹性体的PTFE缓冲密封在前期和后期性能试验中的摩擦力,以及整个耐久试验后的截面形状分析。这两种缓冲密封都与相同的活塞杆密封组合使用。
PTFE缓冲密封显示出相对较低的摩擦力。PTFE元件在两个方向都受到挤出,因为它在两个方向上都具有密封性,并且没有像预期的那样释放中间压力。由此导致主活塞杆密封也受到一些挤出,这证实了PTFE缓冲密封在耐久试验期间不能有效地降低峰值压力。
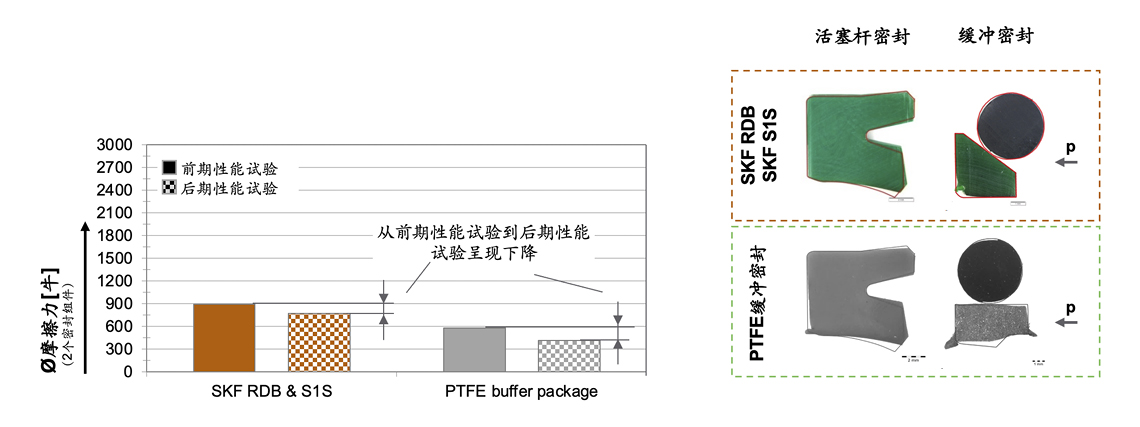
与PTFE缓冲密封相比,SKF RDB显示出略高的摩擦力。但与其他形状的缓冲密封相比,它仍然处于非常好的水平(见图11)。与PTFE缓冲密封相比,RDB在前期和后期性能试验之间的摩擦力下降幅度较小,这是由于硬质聚氨酯滑环的耐磨性和抗挤出性较好。
图13显示了在长时间试验中,两种滑动密封在50巴返行程系统压力下的中间压力。可以看出,PTFE缓冲密封立即积累了中间压力,达到了数倍的系统压力,这是其不具备释压能力的结果。SKF RDB则在50到400巴之间的几个压力段中显示出从无到低的中间压力积累。
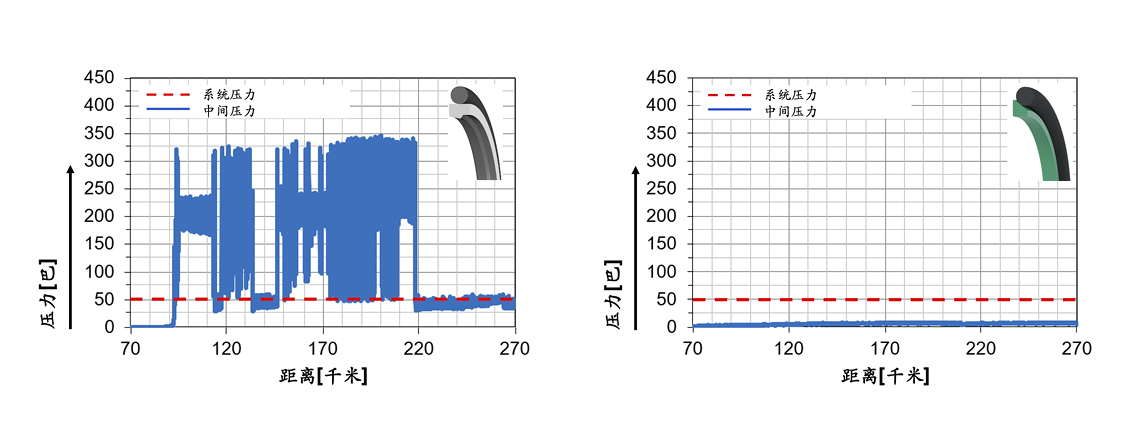
总结与结论
本文介绍了活塞杆密封的主要功能以及不同的缓冲密封的工作原理。通过内部试验台研究的结果,可以透彻地解释缓冲密封和活塞杆密封对液压系统效率的影响。
结果清楚地表明,根据运行参数选择正确的缓冲密封类型非常重要。带有热塑性挡圈的唇型缓冲密封(HDB)可应对非常高的压力。但是以O型圈为弹性体的滑动密封(RDB)在抗挤出性方面存在局限性,尤其是质量不高的PTFE材料会导致超出可接受范围的挤出,因此,此类密封只能用于中等载荷应用场合。
但重要的不仅是选择正确的缓冲密封类型,还必须根据所选的缓冲密封类型,调整主活塞杆密封和防尘圈。请参阅更多SKF手册和文章,了解有关活塞杆密封组件选择的更多信息。
1.7 HDB 缓冲密封的功能和优点
HDB缓冲密封适用于标准缓冲密封沟槽(ISO 和 JIS),确保了尽可能低的摩擦,保证密封具有更长的寿命。 图14显示了该产品的功能和优点。
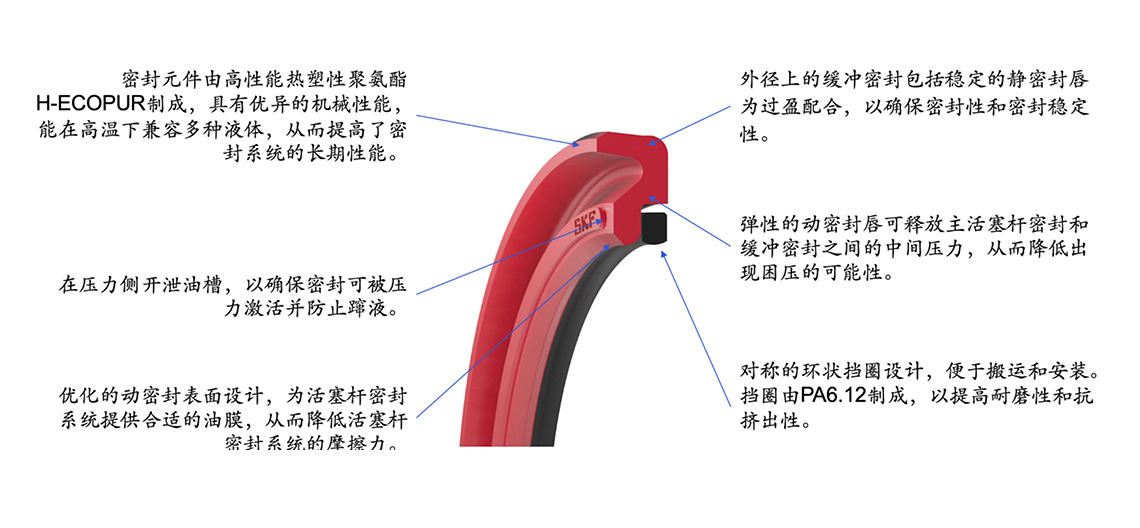
RDB缓冲密封适用于标准缓冲密封槽(ISO 和 JIS),具有出色的性能,且成本低于其它常用的中等载荷缓冲密封。图15列出了该产品的功能和优点。
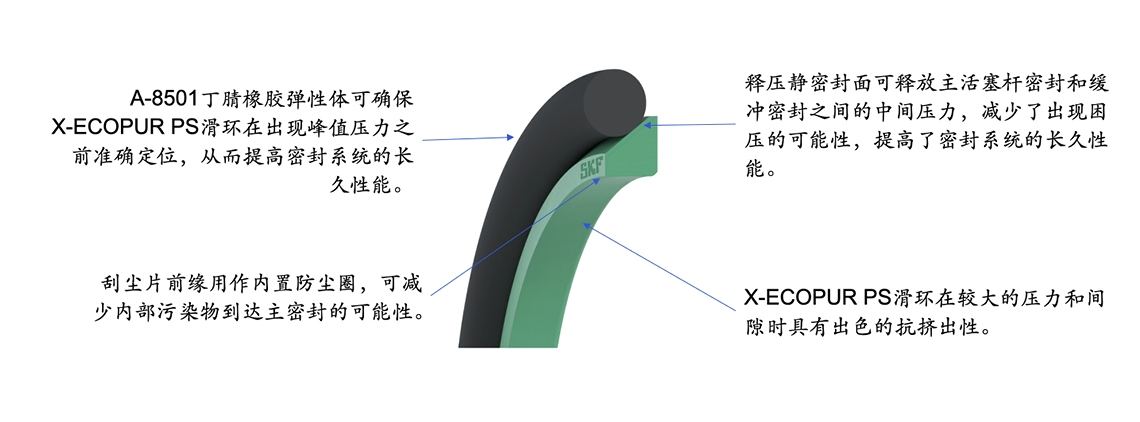
2 参考文献
/1/ SKF Industrial Seals, Hydraulic seals catalogue, 2014-06-18, page 15
/2/ M.Sc. Pat.-Ing Mario Stoll, Reibkraft S1S Prüfprogramm, Institut für Ma-schinenelemente, Universität Stuttgart, März 2017
/3/ Müller, H.K., Nau, B.S.: Fachwissen-Dichtungstechnik, http://www.fachwissen-dichtungstechnik.de
/4/ Dipl.-Ing. Ulrich Nißler, Prof. Dr.-Ing. habil. Werner Haas, Simulation und Versuch bei Hydraulikdichtungen, 14th ISC Tagungsband, S. 497-511