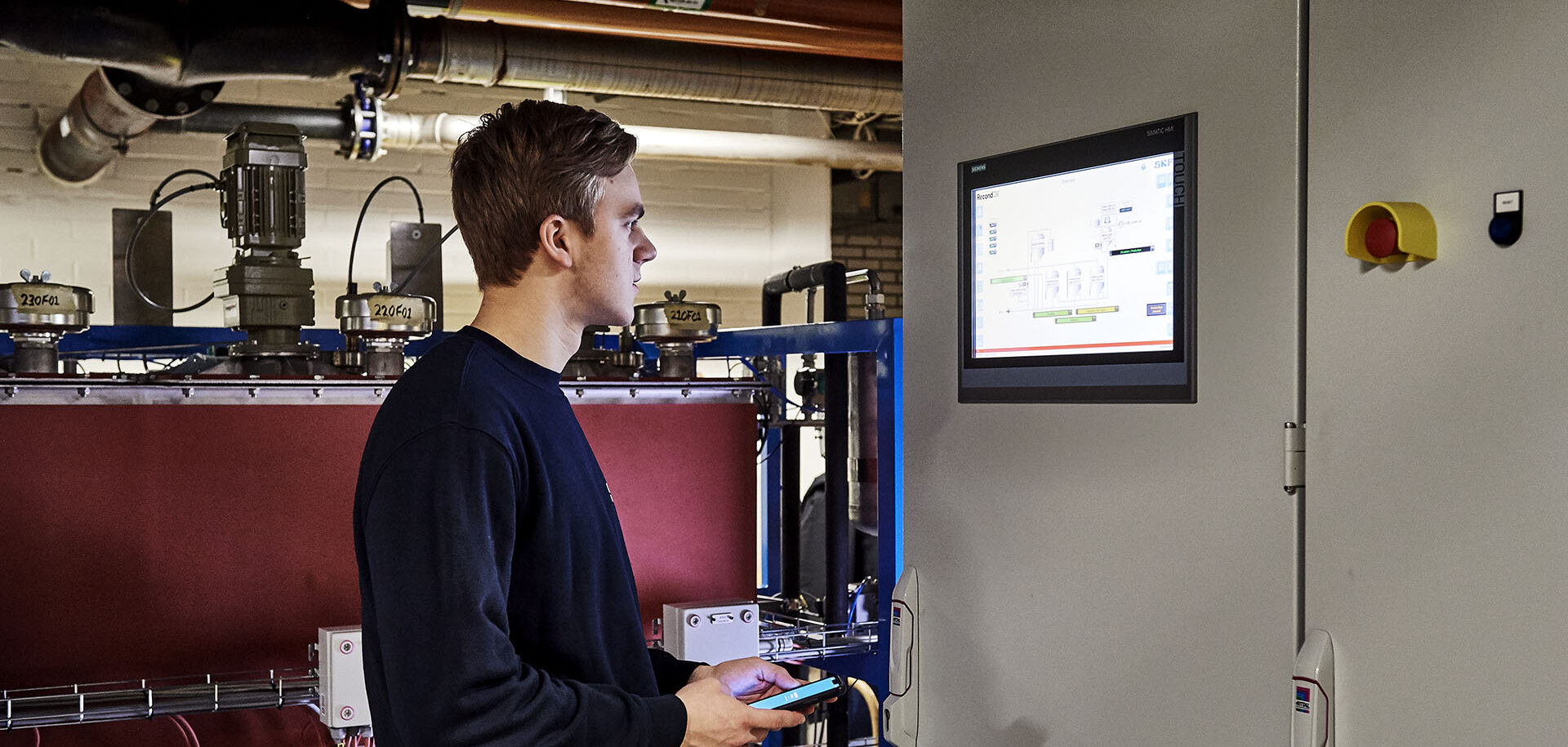
超越过滤——润滑油净化新技术问世
润滑油污染是拖累工业产能的一大因素。对于那些需要较高润滑油清洁度的设备而言,在线过滤可能无法满足其所需性能的要求。通过SKF RecondOil新技术,将润滑油从待解决的污染问题转变成与可靠性提升休戚相关的盟友。
这些污染物会影响润滑油的性能。硬颗粒会造成机器设备或其制造的产品损坏。在高温环境中,污染润滑油会缩聚形成漆膜:这些粘性颗粒会堵塞管道,并附着在摩擦副表面,导致摩擦增加和磨损加速。水和金属颗粒污染物会诱发发生氧化反应,最终导致润滑油发生破坏。
减少以上不良影响的一种方法是定期换油,但是这种策略其自身也存在着问题。首先,新油的 购买价格昂贵。其次,污染润滑油的安全处置也会耗资不菲。此外,频繁更换润滑油意味着额外的维护工作成本和生产时间的损失。如今,各企业正在努力减少其生产活动对环境造成的总体负面影响之际,润滑油消耗量过高肯定是不可取的。
传统的过滤系统
为了延长润滑油的使用寿命并降低润滑油更换频率,大多数大型机器和生产设施都配备了某种类型的净化和过滤设备。工业用户可以从多种技术中选择一种或多种组合的净化和过滤技术,以满足其工艺和操作环境的需要。例如,润滑油可以通过泵送作用后通过过滤器,从而将颗粒捕获而过滤出来,也可以使用特殊过滤材料来吸收润滑油中的水分。
这种系统是用户用来抵御润滑油污染的第一道防线。它们通常布置在润滑油箱和机器设备之间,可以有效地清除直径小至几微米的颗粒。
然而,在线过滤确实存在较大的局限性,特别是对于那些追求更高润滑油清洁度的用户而言。过滤器不可避免地限制了润滑油的流量。过滤器越精细,阻力损失就越大,使用成本也就越高。在过滤器孔径减小的情况下,为了保持润滑油的流量,用户必须安装更大的过滤器,并使系统在更高的压力下运行,这会导致更高的能耗和更高的过滤器更换成本。此外,还包括对使用过的过滤器等有害废物进行环境无害化处理的费用也会增加。
避免此类过滤问题的一种方法是采用离线旁路系统。它们就像人体的肾脏一样工作,将润滑油从油箱中抽泵出,然后通过专门的净化回路进行循环净化处理。由于离线旁路过滤系统与使用润滑油的机器之间是分离开来的,因此离线旁路过滤系统可以按照自己的速度工作,持续不断地对润滑油进行处理,以逐渐降低和减少润滑油的污染。
离线旁路过滤技术还有其它多种不同的替代技术方法,例如:离心过滤系统,使润滑油高速旋转,从而将诸如水等比重较大的物质分离出来。静电过滤器则采用高压电场,吸附带有极性的磨损或油泥/漆状物等颗粒物,将其从润滑油中分离出来。
在当今的关键生产应用中,企业通常同时安装在线和离线旁路的组合式过滤系统,目的是尽可能多地捕获润滑油中的污染物,以保持润滑油性能并延长换油周期。但是,无论企业在传统过滤技术上投入多少资金,仍然会有一些污染物成为“漏网之鱼”。
在典型的润滑油油样中,纳米级颗粒提供的比表面积占所有污染物的比表面积的80%。
Thomas Persson
Process development manager, SKF RecondOil.
小颗粒,大难题
传统过滤技术最大的弱点是对极微小的颗粒束手无策。高效机械过滤系统可以非常有效地去除小至几微米的颗粒。但是对于颗粒直径微小至“纳米级”就会面临着截然不同的挑战。这些颗粒非常微小,肉眼看不见,甚至难以用标准的润滑油分析设备检测出来。即使是极为精细的传统过滤器也无法捕获这些微小颗粒。这些“纳米级”颗粒的数量,如果不加以控制,就会在润滑油系统中累积得越来越多。
尽管纳米级颗粒的尺寸很小,但它们对润滑油性能劣化却有着决定性的影响。这通常是因为它们在大多数工业润滑油的总污染负荷中占了很重要的比重。研究表明,在典型的润滑油油样中,纳米级颗粒提供的比表面积占所有污染物的比表面积的80%。发生氧化反应的地方就处于润滑油和污染物表面之间的界面上,由于氧化是导致润滑油老化的主要原因,因此减小纳米级颗粒提供的比表面积确实是至关重要的。
纳米级颗粒也会造成磨损。球轴承的运动表面之间的润滑油膜厚度有时会小于500纳米,因此即使是远小于1微米的颗粒也足以破坏润滑油膜,可能导致表面损坏。
就在不久之前,设备人员对于去除润滑油中的纳米级颗粒仍然是一筹莫展。人们可以使用极为精细的机械过滤器的滤芯来捕获小于1微米的颗粒,但这些过滤器可能会滤除那些对于润滑油性能和使用寿命至关重要的添加剂,进而对润滑油的性能造成损害。
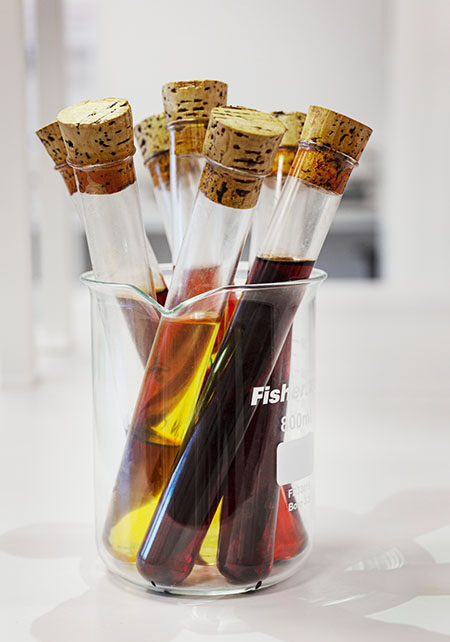
双分离技术(DST)
今天,工业用户可以利用一种SKF新推出的、与之前方法不同的方式: RecondOil双分离技术(DST),来净化他们的润滑油。这是根据最初在生物化学领域中开发出来的,现已应用于工业应用的一种原理而开发出来的一种方法。通过将化学分离和机械分离有机组合在一起的专利分离技术,可以有效地去除润滑油中纳米级颗粒和水分,而不会损坏润滑油及其含有的重要添加剂。
双分离技术(DST)并不会将传统的润滑油过滤器淘汰掉,而是仍然需要它们去除润滑油中较大尺寸污染物。但是,该技术能够捕获那些超出过滤器的过滤能力的微小颗粒。其中,包括那些会造成润滑油发生不可逆的氧化和老化的纳米级颗粒。
双分离技术(DST)的核心是“分离助剂”,将这种专用的化学品按精确的剂量添加到盛放在反应容器中的污染润滑油内。这是一个精细的工艺过程:需要以适当的速度,将适量的分离助剂加入混和到特定温度的润滑油中,且需要让混合物沉降合适时间。
分离助剂可吸附污染物(小至纳米级颗粒),同时保持添加剂完好无损。污染物之间发生聚结后从润滑油中分离出来,留下的清洁润滑油可以进行使用,并且这种再生可以一次次地反复进行。在实际运行条件下进行的测试结果表明,这种方法可以将极小颗粒污染物(小于<0.2微米)的数量减少90-99%。
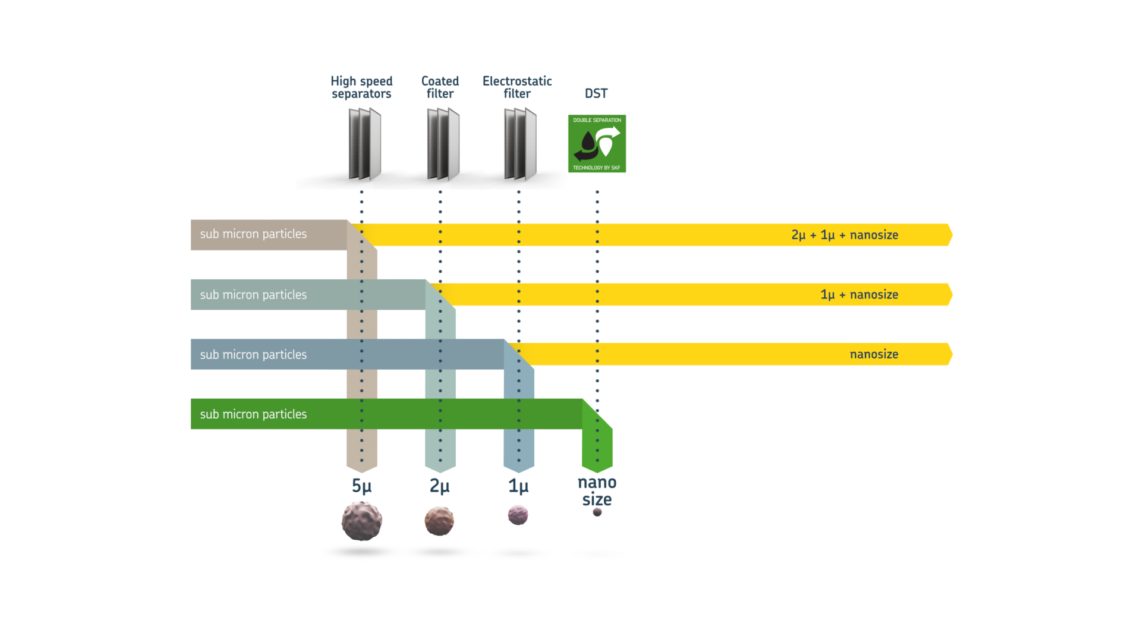
润滑油的循环使用
双分离技术(DST)能够消除许多与污染有关的问题。使用纳米级清洁度的润滑油,可减少设备的磨损和损坏,使设备的使用寿命更长,所需维护更少。工艺流程不再受润滑油性能随时间逐渐衰变下降的影响,从而使工艺流程变得更加稳定和具有可预测性。
实际上,即使是从未使用过的新润滑油,在生产和运输过程中也会有少量污染物侵入,因此在某些应用中,经过双分离技术(DST)处理的纳米级清洁度水平的润滑油,在与清洁度水平相关的性能方面要优于新润滑油。通过双分离技术(DST),润滑油成为提升可靠性的助手,而不是需要解决的反复出现的污染问题。
随着时间的推移,双分离技术(DST) 产生的影响会更加深远。由于该技术去除了润滑油中的纳米级颗粒,因此可以大幅度延缓润滑油氧化——氧化是润滑油发生老化的主要原因。这就意味着这些润滑油几乎可以无限期地重复使用。如果润滑油得到重复利用,那么对原油蒸馏、精炼、运输和分子层面上的深加工的需求就会减少,受到污染的润滑油进行处置的需求也会减少。这样一来,工业润滑油就从昂贵的消耗品转变成在经济和环境方面具有可持续性的循环资源。
将润滑油作为一种服务
SKF基于设备性能表现的合同,就是客户根据其实际运营绩效与预先设定的关键绩效指标(KPI)之间的对比情况来支付费用,关键绩效指标(KPI)包括实现的产能、减少的停机时间、使用能耗或其他相关参数。客户和SKF都能从最大限度地提高设备生产率、可靠性和效率中获益,而不是购买设备和润滑油的传统商业模式。