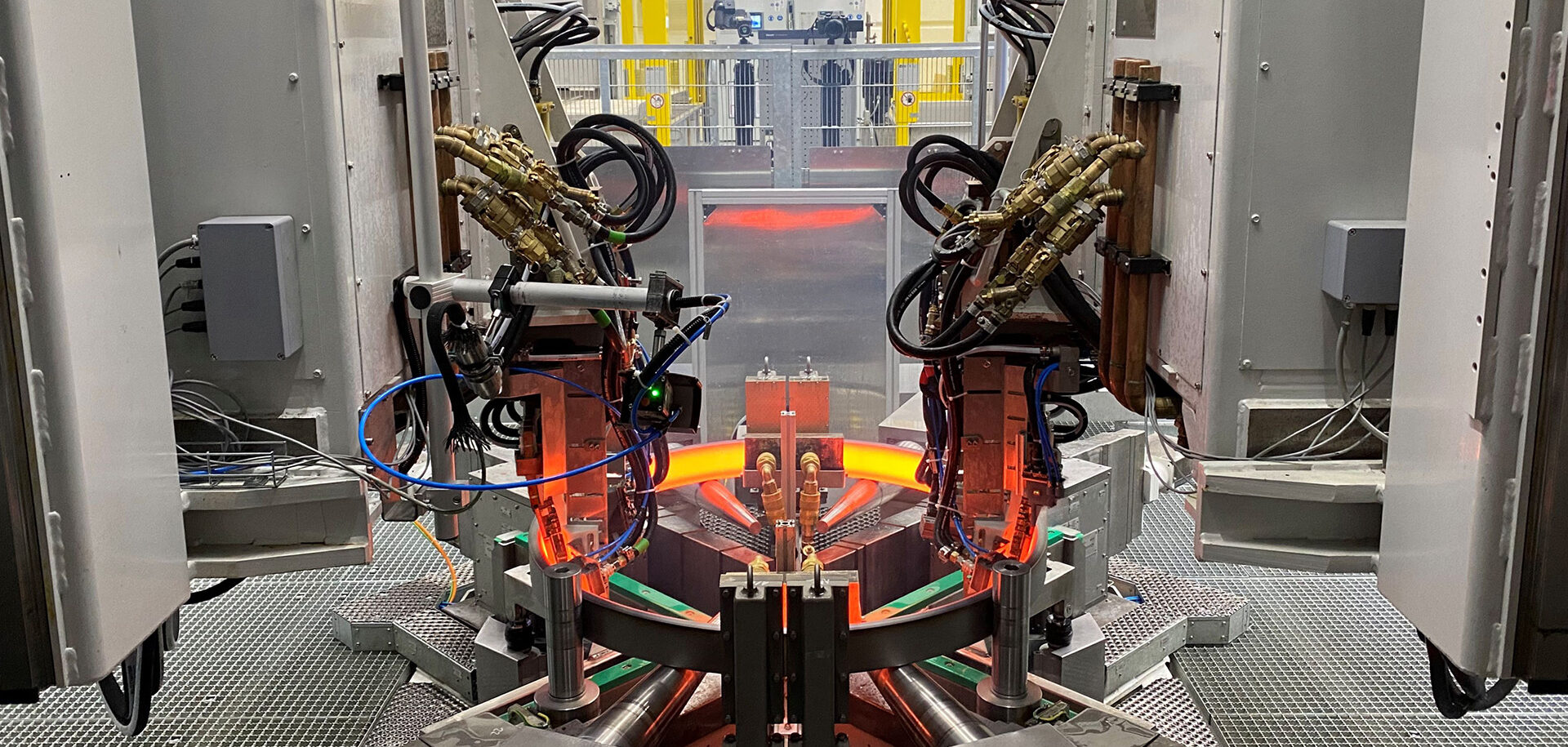
De la trempe traditionnelle à la trempe sélective
Mise en service prochaine d’une technologie de trempe rapide et économe en énergie.
Pour assurer de bonnes performances et une longue durée de vie, les matériaux utilisés pour les bagues de roulement doivent répondre à des objectifs contradictoires. Ils doivent être, d’une part, durs pour résister aux charges imposées par les éléments roulants et, d’autre part, résistants pour ne pas se fissurer sous la pression. Les fabricants se sortent du dilemme en produisant des bagues à partir d’un matériau relativement tendre, puis en les traitant pour créer un composant dur et résistant à l’usure, conciliant les propriétés antagoniques que sont la dureté et la ténacité.
On peut procéder de plusieurs manières, mais presque toutes les méthodes demandent l’application d’une grande quantité de chaleur. La trempe est traditionnellement effectuée dans un four spécialisé. Néanmoins, cette solution peut ralentir les processus et les rendre salissants et extrêmement énergivores. Ce sont des effets non souhaitables dans un monde où les fabricants de roulements – et leurs clients – sont en quête d’une production plus rapide, plus flexible, d’un meilleur rapport coût/efficacité et émettant le moins de CO2 possible.
Importance de l’impact environnemental
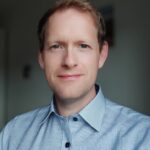
« Nos clients du secteur des énergies renouvelables sont particulièrement intéressés par l’impact environnemental des produits qu’ils achètent, car ils cherchent à décarboner leurs propres chaînes logistiques », explique Michael Wendel, responsable Induction Hardening Technicum chez SKF, à Schweinfurt en Allemagne.
La trempe par induction est une alternative au four. Avec cette solution, un puissant champ magnétique alternatif chauffe la surface de la bague. La méthode est rapide et économe en énergie, car elle permet des temps de traitement courts, un échauffement localisé et ne consomme pas d’énergie quand elle n’est pas utilisée. De plus, le processus est instantanément ajustable, ce qui permet aux fabricants de contrôler avec précision la profondeur de la couche dure à la surface.
La trempe par induction a été largement adoptée pour la production de roulements. Les petites bagues mesurant jusqu’à environ 500 mm de diamètre sont trempées « en statique », à l’aide d’une bobine d’induction qui les entoure et qui chauffe toute leur surface. Pour les bagues les plus grandes, d’un diamètre de plusieurs mètres, les fabricants ont recours à la technique dite « au défilé ». Celle-ci fait appel à une bobine et à un système de trempe par pulvérisation qui balaye la surface de la pièce, chauffant et refroidissant une petite zone à la fois.
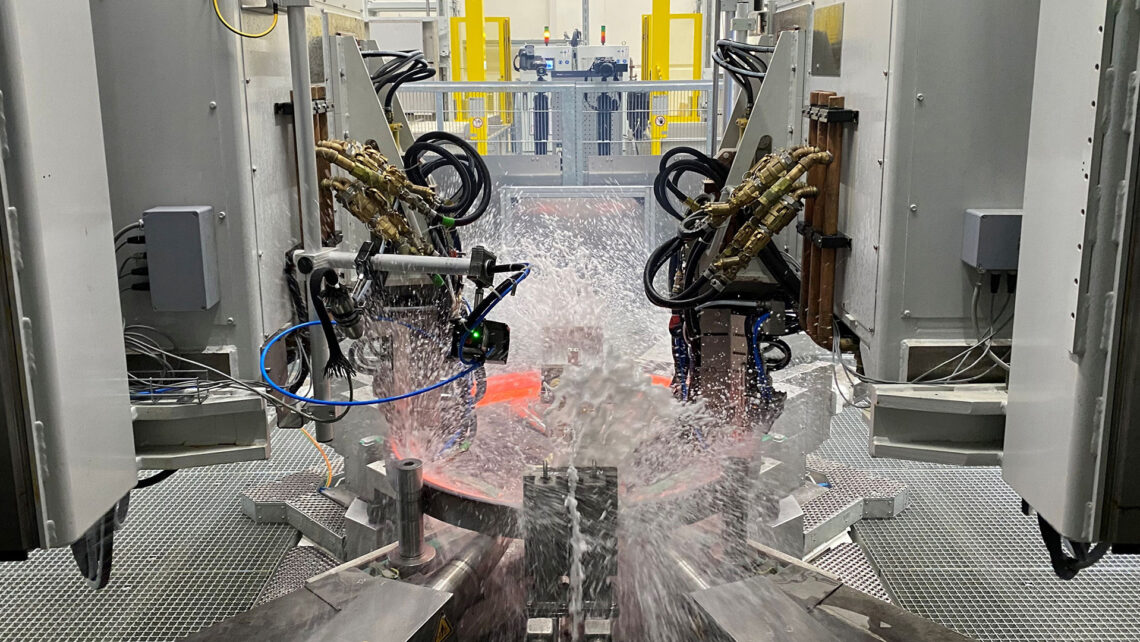
Combler le manque
Jusqu’à récemment, cependant, la boîte à outils de la trempe par induction des fabricants de roulements n’était pas complète. Les roulements de moyennes dimensions, dont le diamètre varie entre 500 mm et 1,6 m environ, sont trop grands pour la technologie conventionnelle de durcissement par induction en statique, mais trop petits pour les inducteurs au défilé.
Nos clients du secteur des énergies renouvelables sont particulièrement intéressés par l’impact environnemental des produits qu’ils achètent.
Michael Wendel, responsable Induction Hardening Technicum chez SKF, à Schweinfurt en Allemagne.
Depuis 2017, une équipe du Centre de développement de la fabrication SKF à Schweinfurt cherche un moyen de combler ce manque. Son projet, réalisé avec le soutien financier du ministère fédéral allemand de l’Économie et de l’Action pour le climat, est désormais prêt à entrer dans sa prochaine phase.
Baptisé Induflex, le système de l’équipe SKF est conçu pour permettre la cémentation en statique des bagues de roulement d’un diamètre compris entre 450 et 1 800 mm. La bague est fixée sur une machine et tourne rapidement devant deux bobines d’induction montées chacune sur un bras articulé piloté par ordinateur. Le bras ajuste constamment la position de la bobine, la maintenant à une distance précise de la bague au moment où le matériau de celle-ci chauffe et se dilate. Une fois la température souhaitée à la surface atteinte, une « douche » fixée sur les bras est activée pour tremper le matériau.
« Comparé à la cémentation classique dans un four, le procédé Induflex est plus propre, plus rapide et beaucoup plus économe en énergie, estime Michael Wendel. Tremper une bague de 512 kg sur un système Induflex ne prend que quelques minutes et ne consomme que 81 kWh d’énergie, soit au minimum deux ordres de grandeur de moins que la cémentation [au four]. »
Des sources d’énergie renouvelables
Étant donné qu’Induflex ne chauffe qu’à partir d’électricité, le processus peut être alimenté par des sources d’énergie renouvelables, ce qui réduit son empreinte carbone. Les roulements de moyennes dimensions sont montés dans un large éventail de machines industrielles, mais le secteur des énergies renouvelables constitue actuellement un domaine de croissance majeur. « Les éoliennes sont équipées de roulements de ces dimensions dans leurs rotors et leurs multiplicateurs. »
Cette méthode de trempe par induction présente d’autres avantages écologiques par rapport aux technologies de trempe classiques. Elle ne demande pas de gaz de process ou de produits chimiques tels que l’azote, le gaz naturel, le méthanol ou l’ammoniac. « Cela simplifie également la chaîne logistique, un critère qui pèse de plus en plus en raison de la récente volatilité des prix et des problèmes de disponibilité de ces produits », souligne Michael Wendel. La trempe par induction pourrait également permettre de recourir à des aciers pour roulements moins alliés et d’un bon rapport efficacité-prix, à l’empreinte carbone plus réduite, ajoute-t-il.
Induflex promet de simplifier la vie des fabricants. En appuyant simplement sur un bouton, les bras articulés pilotés par ordinateur qui déplacent les bobines d’induction peuvent être reconfigurés en vue de tremper des bagues de dimensions et de profils différents. Ceci élimine la nécessité d’un outillage spécifique et permet aux usines de produire de petits lots et de passer facilement d’un produit à l’autre.
Ces quatre dernières années, Michael Wendel et son équipe ont peaufiné le processus Induflex et soumis des prototypes à des essais rigoureux. « Nous avons obtenu de très bons résultats. Le processus produit des surfaces dotées d’excellentes propriétés, notamment une microstructure affinée, des contraintes résiduelles de compression et une dureté élevée. Ceci devrait permettre d’obtenir des bagues de roulement plus résistantes à la formation des fissures et à leur propagation. »
Prêt pour le service
Les recherches sont maintenant passées au stade de la production de prototypes complets. Les éléments sont intégrés à des roulements et font l’objet d’essais approfondis. « À ce jour, les résultats de la phase d’essai sont très prometteurs », estime Michael Wendel. Les essais internes devraient se poursuivre jusqu’à la fin de l’année. SKF collabore également avec un petit groupe de clients pour confirmer que les roulements traités par Induflex conviennent bien à leurs applications.
En attendant, des travaux sont en cours pour industrialiser complètement le processus. « La première machine Induflex a été créée pour les travaux de développement. Elle intègre des commandes et des instruments dont on n’a pas besoin sur une machine de production. Elle n’a pas été conçue pour faire partie d’un environnement de production au rythme soutenu. »
Lorsque les travaux de développement seront terminés début 2024, des machines Induflex entièrement opérationnelles seront installées sur les sites de production SKF du monde entier. « Nous sommes en train d’organiser le déploiement mondial de cette technologie dans les usines qui produisent des roulements pour le secteur des énergies renouvelables », conclut Michael Wendel.
Techniques de traitement de surface des bagues : de la nitruration à la trempe sélective
Avec l’aide de l’État
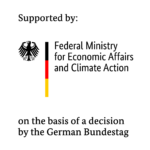