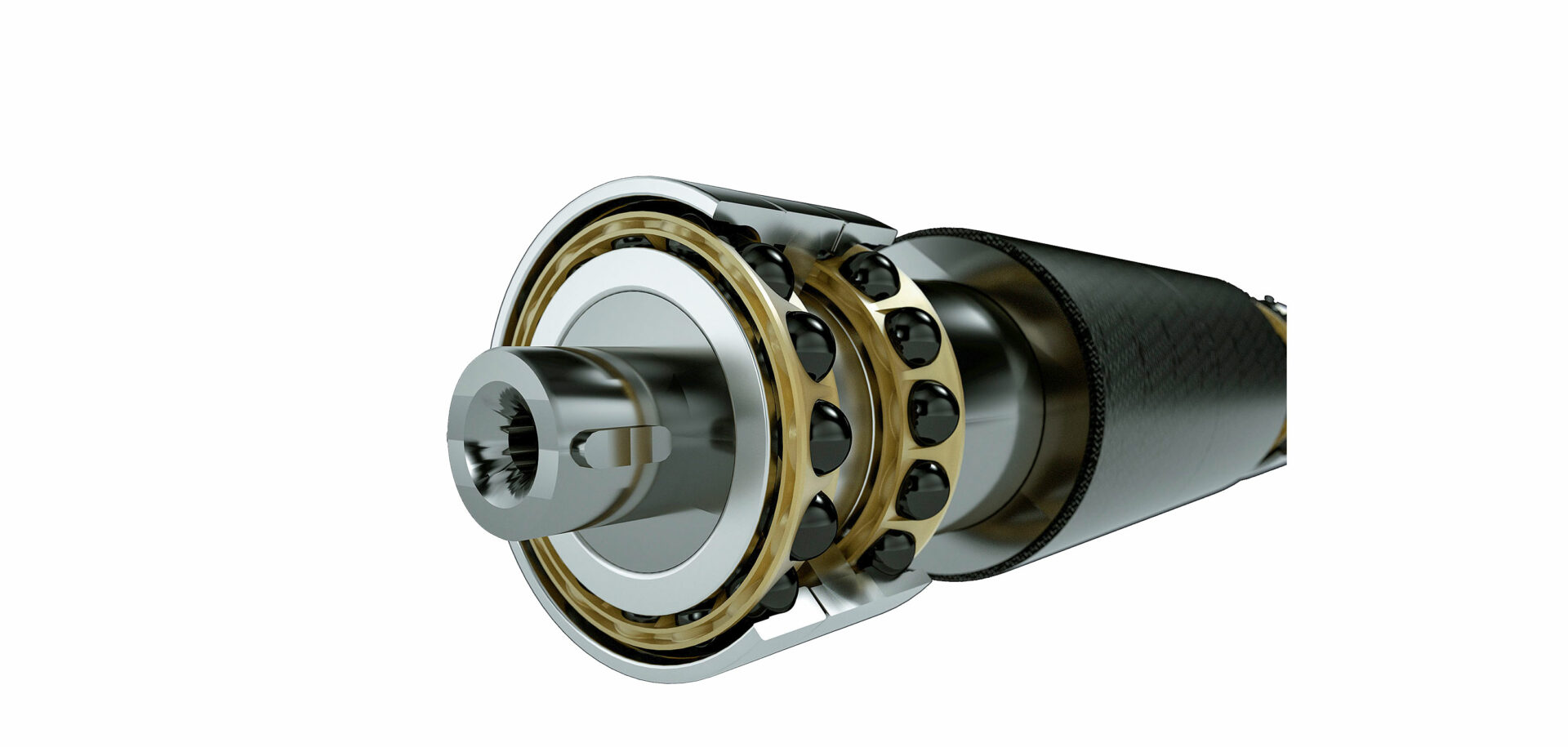
陶瓷混合轴承在 严苛条下的优势
陶瓷混合轴承在润滑不良和污染条下展示出良好性能,但对其基础原理及对性能的影响仍然缺乏了解。通过专门的试验和建模,SKF对陶瓷混合轴承的摩擦学有了更深入的见解。
陶瓷混合轴承具有轴承钢制的轴承圈和轴承级氮化硅(Si3N4)制的滚动体,它已经越来越广泛地应用于各种严苛的应用环境中[1-4] ,如高速、无油空调和制冷压缩机、通用流体机械、电动机器和齿轮箱。在一些上述应用中,边界或混合润滑条件和固体颗粒污染都会影响轴承性能。在边界或混合润滑条件下,轴承滚道表面会对早期表面疲劳和来自表面的疲劳裂纹变得很敏感,具体取决于运行条件以及作用在接触表面的边界摩擦系数和磨损情况[5, 6]。滚道表面的失效风险随着疲劳损伤的积累而升高。在受污染的环境中,嵌入滚动接触面的固体颗粒形成边缘凸起的压痕,即便轴承是在良好的全油膜状态下,这种压痕也会破坏润滑膜。这些较大但处于局部的表面压痕会导致早期表面疲劳[7, 8]。本文列出了专门试验和建模结果,来比较陶瓷混合轴承与全钢轴承的物理机理和性能,首先比较的是薄油膜条件下的典型轴承表面,然后比较了较大压痕形成的特点。
润滑不良条下的表面性能
试验证据显示,在边界或混合润滑条件下通过使用陶瓷混合轴承能够获得突出的性能益处 [1-4],包括提高表面疲劳抗性[3]。借助滚动轴承疲劳试验,以及表面疲劳和磨损组合模型([5]中做了介绍),本文详细考察了在润滑不良条件下,混合滚动接触面的性能[6]。研究还发现,混合接触面表面疲劳抗性的显著提高,无法只通过全钢与混合接触面之间存在的一些粗糙度参数的正常差异来解释。在专门试验中,混合接触面的有效边界摩擦系数相较于全钢轴承显著降低(降低50%),必须将这一因素考虑在内[6]。
试验是在垂直摩擦试验台(图1)按照表1中的试验条件进行的,采用圆柱推力滚子和钢制/Si3N4的垫圈来代表全钢或者混合接触配置,能表现出更高的循环和更快的表面疲劳发展。为避免试验中由于使用太硬的陶瓷平垫圈造成磨损,对其表面进行了抛光,因为陶瓷混合轴承中的陶瓷滚动体的典型表面粗糙度是非常低的。在数字仿真中考虑了钢和陶瓷垫圈之间的表面粗糙度的差异。对钢接触面和混合接触面各进行了总长6小时的四次试验(在2小时和4小时处暂停)。试验中用光学表面光度仪(WYKO)对滚子进行了测量,并用内部开发的软件来量化表面疲劳面积。因为在6个小时测试时间内,混合接触面的钢滚子没有明显的表面损伤,所以又进行了97个小时的更长时间的试验(在37和60小时处暂停)。
图2列出了在上述条件下,混合和全钢接触面的表面疲劳面积的测量数据与数字仿真(使用基于疲劳的模型[6]和疲劳-磨损组合模型[5])的关联性的主要结果。可以明显观察到全钢接触面随时间推移出现表面疲劳的逐渐积累,而混合接触面几乎未出现表面疲劳。还可看到具有混合接触面典型磨损率的表面损伤/磨损组合模型的结果(蓝色曲线)符合试验数据,略好于假设没有磨损的模型的结果(黑色曲线)。
混合和全钢接触面的微凹面积的数字仿真与测量数据之间的关联性提示,平均来讲,全钢与混合接触面的摩擦系数比值大约为2,这部分解释了后者表面疲劳抗性更好的原因。在以前的试验中也获得了这个平均比值[7, 8]。除了较低的边界润滑摩擦,混合接触面的表面疲劳抗性更好的原因还在于Si3N4部件比全钢部件的粗糙度更小、粗糙度偏度负值更大(即深谷超过高峰)。
受污染环境中的表面自我修复属性
尽管对全钢轴承做了大量研究,研究与压痕有关的损伤演变和表面疲劳机理的一大难点是压痕形成的随机属性。控制压痕的数量、几何形状和位置颇具挑战性。这就是为什么许多研究采用人工压痕。采用洛氏球压头在轴承滚道上制造的压痕,常常被用于研究全钢轴承在滚动/滑动条件下的疲劳寿命缩减和损伤过程。观察到在相对滚动方向的压痕的后边缘开始出现剥落。更多滑动或高表面摩擦牵引力将加快表面裂纹的生成。裂纹是由在后边缘近表面处发展的最大正交剪切应力所引起的[7, 8]。这些应力的大小取决于压痕的形状、润滑质量、公称接触压力和滚动/滑动量。此外,在出现磨损和其他表面损伤的压痕的前导边缘处,对润滑膜破损进行了建模分析。已发表的有关陶瓷混合轴承在受污染环境中性能的研究寥寥无几。开创性的工作[3]显示出在严重污染油润滑条件下的卓越耐磨性能。研究人员提出了与Si3N4更高的杨氏模量和硬度相关的“自我修复”机理。它在钢部件上的压痕的凸起边缘处产生塑性变形,从而可抑制表面疲劳、剥落和破坏性磨损的产生。
为了进一步探究,本文通过对钢或Si3N4滚动体在钢滚道上的人工压痕进行试验和建模,直接比较了两者的性能[9]。这些压痕是在全钢和陶瓷混合深沟球轴承的内圈上形成的(图3)。然后在同样工作条件下测试轴承。图4的例子采用了极佳润滑(全油膜)和中等接触压力的运行条件。考虑到Si3N4滚珠的杨氏模量,这意味着混合接触面是在名义接触压力稍高的情况下运行的(如表1)。定期中断试验,进行检查和测量,结果显示全钢和陶瓷混合轴承在滚道表面方面和压痕凸起边缘的变化方面有显著差异(图4a)。
全钢轴承凸起的压痕边缘显示出有限的塑性变形和压痕形状改变(图4b)。当压痕的凸起边缘被滚过时,这个有限的变形保持了一定水平的局部压力分布(图5b)。此外,表面上出现了清晰的表面损伤。在预计出现油膜破损的压痕的前导边缘处(图4d),观察到两种机理:因为钢滚珠的表面在滚过压痕时也变得粗糙,表面粗糙和微小压痕形成一些表面粘着磨损和表面塑性变形。在预计应力集中较高的压痕的后边缘,全钢轴承显示出表面粗糙、微小压痕和凸起的压痕边缘形成的表面塑性变形。随着运行时间延长,材料变形并被挤入压痕(图4e),开始出现小的表面裂纹,裂纹随着进一步运行而缓慢扩展。表面疲劳建模[6, 7]指出对应于试验观察到的具体位置,局部轴承圈出现高表面牵引应力和疲劳(图6a)以及裂纹萌生隐患风险(图4b和图4e)。
在运行的早期阶段,陶瓷混合轴承发展出更大和更平的压痕边缘(图4a和图4c)。一开始就在前导边缘观察到轻微磨损消除了表面标记并保持非常光滑的表面(图4f)。 Si3N4滚珠表面也保持了良好状态,并保持了它初始的粗糙度。弹性有限元仿真的结果(图5a)显示出混合接触面出现较高的应力以及因此带来的较高的局部变形,解释了伴随材料被挤入压痕的早期振动硬化(塑性稳定化)。随着运行时间进一步延长,在后边缘也观察到轻微磨损(图4g)。这个快速的轻微磨损再适应了压痕边缘,也改变了它们的斜度(图4a),从而稳定了轻微磨损,让压痕形状不再发展。压力大幅降低,阻止了轻微磨损机理。
尽管陶瓷混合轴承开始时局部压力更高,但压痕形状的再适应将局部压力降低到与该试验条件下的全钢轴承类似的水平(图5b)。除了局部压力的降低,表面疲劳建模[9, 10]表明,在压痕边缘出现压力梯度下降。更重要的是,特别是具体到局部压痕边缘很薄的润滑油膜条件,表面疲劳建模显示表面牵引应力更小,并且疲劳积累或裂纹萌生隐患风险也更低(图6b)。这是由于混合接触面边界摩擦系数更低的缘故[6]。
在同样负荷条件下,确定了全钢和陶瓷混合轴承的压痕寿命(图3)。在最大接触压力更高、油膜更薄的条件下运行的陶瓷混合轴承的压痕寿命比最大接触压力较低、全油膜条件下的全钢轴承更长(图7)。
这些发现看起来违反直觉,但它们显示出陶瓷混合轴承在润滑不良、表面粗糙和摩擦应力条件下的优势(无论它们是由压痕还是整体润滑不良造成的)。此前有报道说,在纯滚动条件下混合接触面在颗粒嵌入和滚过时,最终导致更深的压痕,但本研究显示的机理将能对此予以补偿[11]。这些优势极大地平衡了混合接触面在一定载荷条件下所出现的更高接触压力。不过,在接触压力极高的罕见应用情况下,这个积极的平衡可能会被削弱或降低。 ●
总结
相比全钢轴承,陶瓷混合轴承更不容易出现表面损伤,原因在于轴承级氮化硅的低边界摩擦和有利的粗糙度形状。
在陶瓷混合轴承中,只有钢部会出现轻微磨损,而陶瓷部几乎没有任何改变。
在受污染条下,压痕边缘的轻微磨损、塑性变形和光滑表面的维持让陶瓷混合轴承的局部应力下降。
在油膜破损出现的压痕周围区域,显示出对表面疲劳和与边界润滑条有关的损伤的良好抵抗性,从而使陶瓷混合轴承的压痕寿命延长。
参考文献:
[1] Lewinschal, L., “Bearings for high speed operation”, SKF Evolution, No. 2 1994, pp. 22-26. http://evolution.skf.com/bearings-for-high-speed-operations
[2] Hultman, A., Weimarck, A. K., “Ceramics stand up to harsh realities”, SKF Evolution, No. 4 1998, pp. 25-26. http://evolution.skf.com/ceramics-stand-up-to-harsh-realities
[3] Gabelli, A., Kahlman, L., “Bearings that heal themselves”, SKF Evolution No. 3 1999, pp. 26-28.
http://evolution.skf.com/bearings-that-heal-themselves-2
[4] Morales Espejel, G. E., Hauleitner, R., Wallin, H. H., “Pure refrigerant lubrication technology in oil-free centrifugal compressors”, SKF Evolution, No. 1 2017, pp. 26-30. http://evolution.skf.com/pure-refrigerant-lubrication-technology-in-oil-free-centrifugal-compressors
[5] Morales-Espejel, G.E., and Brizmer, V. (2011), “Micropitting Modelling in Rolling-Sliding Contacts: Application to Rolling Bearings”, Tribol. Trans., 54(4), pp. 625-643.
[6] Brizmer, V., Gabelli, A., Vieillard, C., and Morales-Espejel, G.E. (2015), “An Experimental and Theoretical Study of Hybrid Bearing Micropitting Performance under Reduced Lubrication”, Tribology Transactions, 58, pp. 829-835.
[7] Morales-Espejel, G.E., Gabelli, A., “The behaviour of indentation marks in rolling-sliding elastohydrodynamically lubricated contacts”, Tribology Transactions, 54, pp. 589-606, 2011.
[8] Morales-Espejel, G.E., Gabelli, A., “The progression of surface rolling contact fatigue damage of rolling bearing with artificial dents”, Tribology Transactions, 58, pp. 418-431, 2015.
[9] C. Vieillard, Y. Kadin, G.E. Morales-Espejel, A. Gabelli (2016), “An experimental and theoretical study of surface rolling contact fatigue damage progression in hybrid bearings with artificial dents”, Wear, pp. 364-365, pp. 211-223.
[10] Morales-Espejel, G. E., Brizmer, V., Stadler, K., “Understanding and preventing surface distress”, SKF Evolution, No 4 2011, pp. 26-31. http://evolution.skf.com/understanding-and-preventing-surface-distress
[11] V. Strubel, N. Fillot, F. Ville, J. Cavoret, P. Vergne, A. Mondelin, Y. Maheo., “Particle entrapment in hybrid lubricated point contacts”, Tribology Transactions 2016, VOL. 59, No. 4, pp. 768-779.