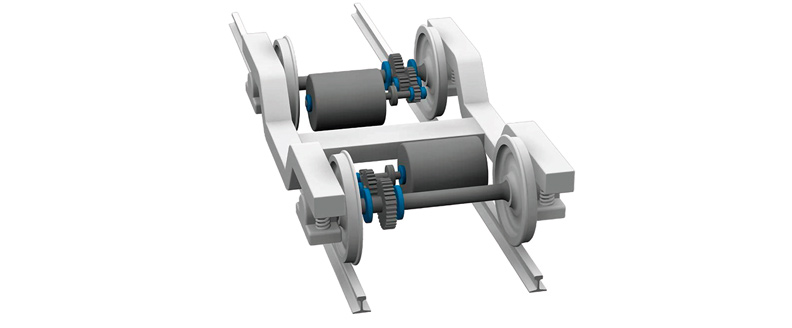
Lösungen für Antriebssysteme
Antriebssysteme für Anwendungen bei Schienenfahrzeugen, wie Getriebe und Fahrmotoren, müssen leistungsfähig, äußerst zuverlässig und kosteneffizient sein, Umweltvorschriften erfüllen und einen geringen Wartungsbedarf haben. Die Anforderungen an diese Anwendungen sind aufgrund des hohen Gewichts von Schienenfahrzeugen und der Notwendigkeit langer Wartungsintervalle viel höher als in anderen Industriezweigen. All dies verlangt nach speziellen Lagern und Lagereinheiten, dem Einbau von Sensoren, dem Einsatz von Zustandsüberwachungssystemen und der Durchführung entsprechender Dienstleistungen.
Zusammenfassung
Antriebssysteme von Schienenfahrzeugen übertragen das Drehmoment des Fahr- oder Verbrennungsmotors, der normalerweise bei höheren Drehzahlen läuft, mittels eines 1-, 2- oder mehrstufigen Getriebes auf den Radsatz. SKF hat eine Vielzahl neuer Lösungen für Schienenfahrzeuge entwickelt, die deren Zuverlässigkeit erhöhen, Wartungsintervalle verlängern und für Kosteneffizienz sorgen. Vor Kurzem hat SKF ein Handbuch über Antriebssysteme veröffentlicht, das Lager und Lagereinheiten, Sensoren, Zustandsüberwachung und Dienstleistungen behandelt.
Links
SKF Railway Technical Handbook
Ansprechpartner Verkauf
Gottfried Kuře, Gottfried.Kure@skf.com
Antriebssysteme von Schienenfahrzeugen übertragen das Drehmoment des Fahr- oder Verbrennungsmotors, der normalerweise bei höheren Drehzahlen läuft, mittels eines 1-, 2- oder mehrstufigen Getriebes auf den Radsatz.
SKF als ein führender Lieferant der Bahnindustrie weltweit bietet hierfür eine große Auswahl an Kundenlösungen. Im Laufe der Jahre hat sich SKF ein umfassendes und fundiertes Wissen in diesem Bereich zugelegt und ein einzigartiges Angebot an Produkten und Lösungen für Antriebssysteme entwickelt, das die hohen Ansprüche von Bahnanwendungen erfüllt. Hierunter fallen Lager, Dichtungen, Schmierstoffe und Schmiersysteme, Mechatronik-Bauteile und Dienstleistungen.
Historische Anwendungen
Geringere Wartungskosten, kleinere Einbauräume und höhere Zuverlässigkeit waren schon immer die treibenden Hauptfaktoren für die Umsetzung neuer Lagerlösungen bei Getrieben und Fahrmotoren.
Die frühesten Konstruktionen besaßen ölgeschmierte Gleitlager, deren Ölstand tagtäglich überprüft und ggf. nachgefüllt werden musste. 1918 vermeldete SKF, dass durch den Einbau winkelbeweglicher Kugellager anstelle der Gleitlager die Lagerwartungskosten bei Straßenbahnen um 25 bis 70 Prozent gesenkt werden könnten (Bild 1).
Geschwindigkeit
Im Laufe der Zeit hat die Zuggeschwindigkeit immer mehr zugenommen. Die Fahrzeuggeschwindigkeit und ein vorgegebener Raddurchmesser bestimmen die Drehgeschwindigkeit der Getriebeabtriebswelle und der zugehörigen Lager. Ein Vielfaches dieser, von der Getriebeübersetzung vorgegebenen Drehgeschwindigkeit beträgt die Getriebeeingangs- und Fahrmotordrehzahl. Das Produkt der beiden Faktoren Fahrmotordrehzahl (n) und mittlerer Lagerdurchmesser (dm) ist ein wichtiger Parameter bei der Auswahl der Lagergröße, Käfigausführung und des Rollensatzes sowie des Schmierstoffs und seiner Viskosität.
Darüber hinaus erhöht sich der Wert n x dm dadurch, dass die Fahrmotordrehzahl aufgrund des Downsizings der Fahrmotorgeometrie zunimmt. Ferner ist es so, dass hochleistungsfähige Fahrmotorausführungen nur mit höheren Motordrehzahlen realisiert werden können. Allerdings beschränkt insbesondere ein Konstruktionsfaktor, nämlich der Abstand zwischen den zwei Rädern, der von der Spurweite abhängig ist, die horizontale Gesamtlänge der Getriebe- und Fahrmotoranordnung.
Leistung
Betrachtet man die historische Entwicklung von Fahrmotoren über eine längere Zeit, so stellt man fest, dass die Leistung schrittweise erhöht wurde. Dies kann man am Beispiel einer typischen vierachsigen Elektrolokomotive deutscher Bauart mit vier Fahrmotoren sehen. Heute ist die Fahrmotorleistung im Vergleich zur ersten Ausführung fast um das Zehnfache höher (Bild 2). Die Motorleistung bezogen auf die Drehzahl hat einen direkten Einfluss auf die Belastungen, die auf die Getriebeeingangswelle einwirken. Bei den heutigen Antriebssystemen geht es in erster Linie darum, die Lagerbelastung möglichst zu reduzieren und den Einsatz von Ölschmierung weitmöglichst voranzubringen.
Wartungsintervalle
Ein wichtiger Trend, der sich wohl fortsetzen wird, ist die Verlängerung der Wartungsintervalle. Ein Vorteil der Nutzung der Drehstromantriebstechnik bei elektrisch betriebenen Fahrzeugen ist der niedrigere Wartungsbedarf, der somit verlängerte Wartungsintervalle zur Folge hat.
Bei Fahrmotorlagern beträgt die erwartete wartungsfreie Zeit bis zur Lebensdauermitte rund 15 Jahre. Heute gibt es bei fettgeschmierten Fahrmotorlagern jedoch verschiedene Lebensdauerbeschränkungen, die ein Erreichen dieses Alters erschweren. Allerdings ermöglichen es verschiedene neue Lagerkonstruktionen, Berechnungsmodelle und Prüfergebnisse, dass dieses Ziel schrittweise erreicht wird. Die neuen Richtlinien von SKF zur Optimierung der Fettgebrauchsdauer können hinsichtlich der Verlängerung der herkömmlichen Wartungsintervalle sehr nützlich sein (Bild 3).
Downsizing-Möglichkeiten
Wie bereits erwähnt, kann eine höhere Fahrmotordrehzahl bei vorgegebener Fahrmotorleistung ein niedrigeres Drehmoment auf der Motorwelle und Getriebeeingangswelle bewirken. Dies verringert die Lagerbelastung und ermöglicht den Einbau kleinerer Lagerausführungen. Darüber hinaus wurden die Lager aufgrund höherer Tragzahlen im Laufe der Zeit immer kleiner konstruiert (Bild 4). Es hat sich gezeigt, dass dies einen äußerst positiven Einfluss auf die Reduzierung der Lagerreibung hat und zu einer höheren Lagerleistungsfähigkeit führt.
Einlaufphase
Ein weiteres Beispiel ist die Weiterentwicklung von Kegelrollenlagerkonstruktionen in Bezug auf niedrigere Betriebstemperaturen während der Einlaufphase. In dieser Zeit wird eine Lagerung mit konventionellen Kegelrollenlagern bei einer hohen, zum Verschleiß führenden Reibung betrieben, die als Temperaturanstieg erkennbar ist.
Eine Lagerung mit aktuellen SKF Kegelrollenlagern zeichnet sich durch eine erheblich niedrigere Reibung, Reibungswärme und einen geringeren Verschleiß aus, vorausgesetzt, die Lager sind richtig montiert und geschmiert.
INSOCOAT Lager und Hybridlager
Die Anforderungen an Fahrmotorlager haben sich mit der Einführung von frequenzumrichtergesteuerten Fahrmotoren als Antriebssysteme beträchtlich erhöht. Kurzzeitige Stromdurchgänge durch das Wälzlager können bereits Schäden verursachen (Bild 6). INSOCOAT Lager und Hybridlager reduzieren das Risiko eines schädlichen Stromdurchgangs durch das Lager in erheblichem Maße.
In Gleichstrom(DC)-Anwendungen wirkt ein INSOCOAT Lager wie ein normaler (rein ohmscher) Widerstand. Die Aluminiumoxidschicht ist ein Isolator; der ohmsche Widerstand R der Schicht ist der wichtige Parameter. Die Durchschlagspannung der Standardschicht wird mit 1.000 V DC angegeben; der Widerstand ist größer als 50 MΩ, was eine ausreichende Isolierung des Lagers sicherstellt.
Hybridlager stellen eine weitere Verbesserung der elektrischen Isoliereigenschaften dar, insbesondere bei den modernen Hochfrequenzumrichtersystemen, da sie mit Wälzkörpern aus für Wälzlager geeignetem Siliziumnitrid ausgestattet sind (Bild 7). Selbst bei sehr hohen Frequenzen zeichnen sich diese Lager durch hervorragende elektrische Isoliereigenschaften aus.
Längere Wartungsintervalle können sich durch Anwendung der neuen optimierten Fettgebrauchsdauer-Richtlinien ergeben. Die wichtigsten Parameter hierbei sind:
- optimiertes Lagerdesign, insbesondere im Hinblick auf Anzahl und Größe der Wälzkörper
- weiter verbesserte Käfigkonstruktion
- Labyrinthdichtungen zum Schutz der Lagerung gegen Verunreinigungen
- spezielle Fettsorte und eingefüllte Fettmenge.
Lagereinheiten für Fahrmotoren
Fahrmotor-Lagereinheiten (TMBU) basieren auf einer kompakten, platzsparenden Konstruktion, die eine wartungsfreie Lösung für längere Wartungsintervalle darstellt. Damit kann entweder die Gesamtlänge des Fahrmotors verkürzt, oder aber die Eisenlängen des Stators und Rotors können in einem vorgegebenen Motorbauraum verlängert werden, um eine höhere Leistung zu erzielen. Dieses Subsystem-Konstruktionsprinzip vereint verschiedene Funktionen in einer einzigen Einheit, wie beispielsweise Schmier-, Abdichtungs- und Haltefunktionen. Der integrierte Flansch erleichtert die Montage.
Bei der SKF TMBU handelt es sich um eine abgedichtete, vorgeschmierte Lagereinheit, die an das Motorgehäuse angeflanscht wird (Bild 8). Ein Spezialfett ermöglicht selbst bei hohen Betriebstemperaturen eine längere Fettgebrauchsdauer. Die Lagereinheit ist mit berührungs- und verschleißfreien Labyrinthdichtungen ausgerüstet. Zudem ist sie erhältlich als Hybridausführung mit keramischen Wälzkörpern, die durch Stromdurchgang verursachte Schäden verhindern, oder aber mit Sensoren bestückt zur Erfassung der Betriebszustände. Zusätzliche Funktionen beinhalten die elektrische Isolierung und die Überwachung von Betriebsdaten wie beispielsweise Temperatur, Drehzahl und absolute Positionierung für die Antriebssystemsteuerung.
Sensoren
Das mit Sensoren versehene TMBU Lagerkonzept (Bild 9) bietet verschiedene Möglichkeiten zur Datenerfassung und Messung: absolute Positionserfassung für Fahrmotorsteuerungen, Drehrichtungserfassung, Drehzahlmessung für Bremssteuerungssysteme und Temperaturmessung zur Überwachung von Betriebszuständen.
In den meisten Fällen werden die Sensoren in das Dichtungssystem des Außenrings der Lagereinheit integriert. Diese Konstruktion bietet verschiedene Möglichkeiten, um Platz zu sparen und die Anzahl der Bauteile zu reduzieren.
Zustandsüberwachung
Bei der Zustandsüberwachung handelt es sich um eine ausgereifte Technologie, die neue Möglichkeiten zur Verbesserung der Betriebssicherheit und Zuverlässigkeit sowie zur Verlängerung der Wartungsintervalle bietet. Durch den Einsatz von Zustandserfassungssystemen (Bild 10) und die Anwendung besonderer Algorithmen bei der Datenverarbeitung können Schäden bereits im Frühstadium entdeckt werden. Dadurch steht ausreichend Zeit für Reparaturen zur Verfügung, bevor größere mechanische Schäden oder Ausfälle auftreten.
Wiederinstandsetzung
Die Wiederinstandsetzung1 von Lagern kann im Vergleich zur Herstellung eines neuen Lagers zu einer erheblichen Senkung der CO2-Emissionen führen. Bei der Wiederinstandsetzung werden bis zu 97 Prozent weniger Energie benötigt als bei der Neufertigung eines Lagers. Durch die Verlängerung der Lagerlebensdauer (Bild 11) wird durch diesen Prozess nicht nur das Verschrotten von Bauteilen, sondern auch der unnötige Verbrauch natürlicher Ressourcen vermieden. Die Spezialisten von SKF können genau beurteilen, ob sich ein Lager für eine Wiederinstandsetzung eignet oder nicht.
Die Wiederinstandsetzung von Lagern trägt in erheblichem Maße zur Optimierung der Lebenszykluskosten bei, indem sie folgende Vorteile bietet:
- erhebliche Kostensenkung im Vergleich zu neuen Lagern
- längere Lagerlebensdauer
- höhere Verfügbarkeit und dadurch Reduzierung des Ersatzteillagerbestands
- Fehlerursachenanalyse und Ermittlung von Korrekturmaßnahmen
- Steigerung der Leistungsfähigkeit durch ein Upgrading während des Wiederinstandsetzungsverfahrens
- Anwendungsfeedback nach Verbesserung der Betriebs- und Wartungstechnik beim Kunden
- Umweltschonung durch Verringerung von Abfallmenge, Rohstoffeinsatz und Energieverbrauch.
Publikationen
SKF hat kürzlich ein Handbuch über Antriebssysteme von Schienenfahrzeugen veröffentlicht. Es behandelt schwerpunktmäßig Fahrmotor- und Getriebelager, Sensoren, Zustandsüberwachung und Dienstleistungen. Man findet darin auch Empfehlungen zur Maximierung der Lagerlebensdauer sowie Hinweise bezüglich Einbau, Wartung und Zustandsüberwachung.
1) Neben dem englischen Oberbegriff „Remanufacturing“ (Wiederinstandsetzung) verwenden manche Betreiber und Hersteller von Schienenfahrzeugen auch die Bezeichnungen „Reconditioning“ (Rekonditionierung) und „Refurbishment“ (Überarbeitung), um besondere Anforderungen zu spezifizieren. „Remachining“ beinhaltet normalerweise Polieren und Nachschleifen. Allerdings scheinen diese Bezeichnungen weltweit nicht eindeutig definiert zu sein.
INSOCOAT und SKF Explorer sind eingetragene Markenzeichen der SKF Gruppe